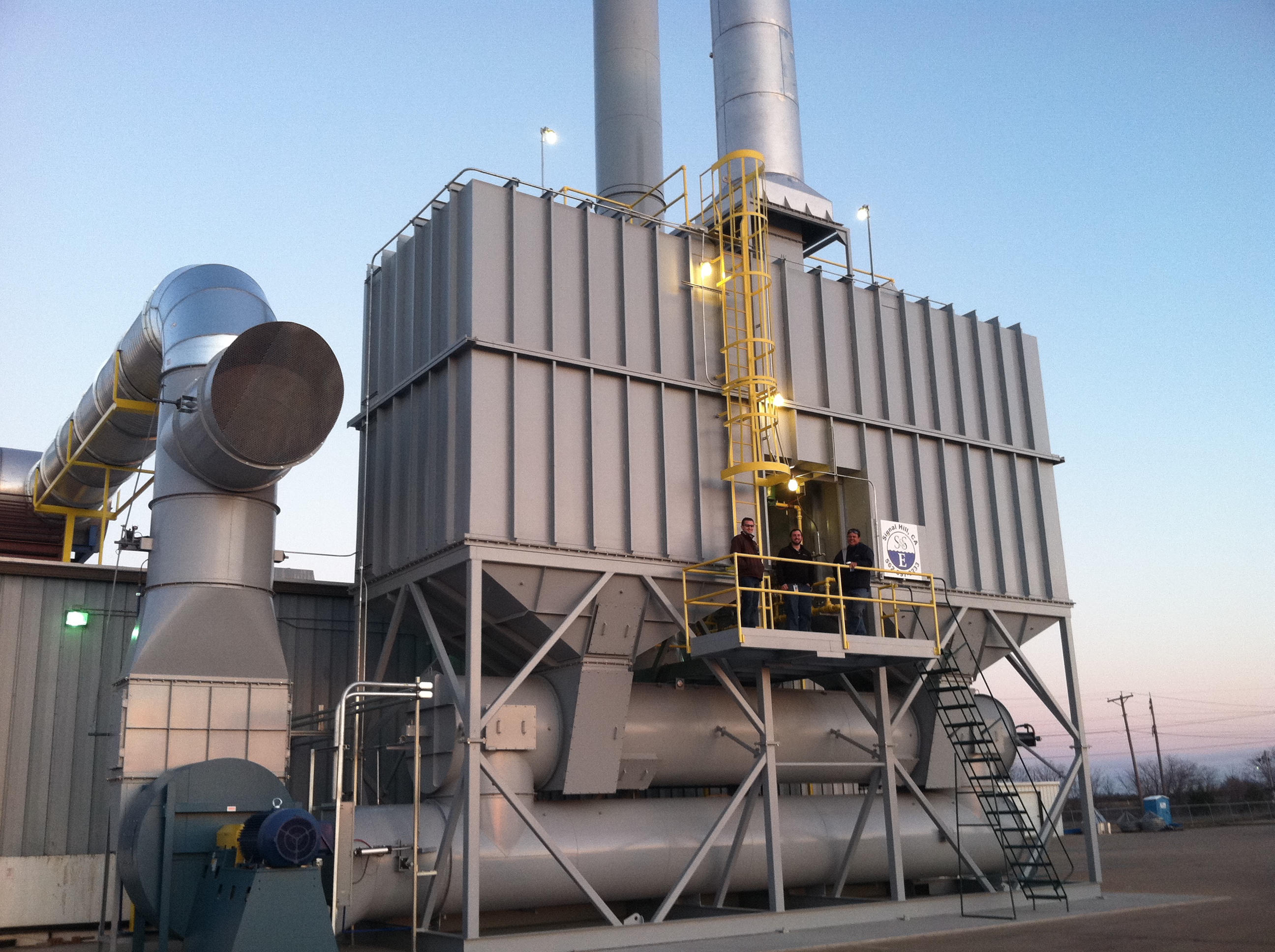
Enclosed Combustion Equipment and Technology
January 3, 2018 1:54 pmEnclosed Combustion Equipment and Technology
A thorough understanding of enclosed combustion technologies will help engineers to select the proper equipment to balance emissions-control performance with efficiency, costs and complexity
Selection of an enclosed combustion solution is a complex process that involves various environmental and operational requirements that are unique for each application. There is great benefit in selecting the correct equipment, since it can translate into decreased capital and operational costs by preventing over-designing or under-designing the equipment. Different technologies offer tradeoffs between initial cost, operating expense and complexity, emissions, fuel efficiency and destruction efficiency. This article describes the main categories of enclosed combustion devices and presents a few of the advantages and tradeoffs to aid in selecting the proper equipment for a particular case.
ENCLOSED FLARES
The simplest enclosed combustion device is an enclosed flare. An enclosed flare is simply meant to hide the flame and does not make a particular effort to increase combustion efficiency or reduce emissions. Enclosed flares provide cooling and combustion air through natural draft. The enclosed flare burner is simple and can be an anti-flashback type, a high-pressure type or a forced-draft type. A forced-draft type of device is used when the process gas has a tendency to produce smoke. It utilizes a blower to provide 20–40% of the stoichiometric air to the fuel gas near the burner tip. Enclosed flares typically operate at around 98% destruction efficiency.
Destruction efficiency is defined as the difference between the amount of pollutants entering the system and the amount of pollutants exiting the system divided by the mass of pollutants entering the system, expressed as a percentage. Depending on the pollutants to be destroyed, a minimum destruction efficiency is needed to meet regulations. Thus, the selection of the combustion equipment depends on the destruction efficiency needed.
In order to reach higher levels of destruction efficiency, we start off with an enclosed flare design and add temperature control and assist gas. This can be called a vapor combustor, or in some cases, a thermal oxidizer. The vapor combustor can maintain higher temperatures in the chamber, which allows it to maintain a destruction efficiency of up to 99.9%. Residence time is typically around 0.7 seconds for these types of combustors.
A thermocouple is used to monitor system temperature and control the opening of the louvers or the flow of assist gas to maintain a desired chamber temperature of 1,400 to 1,800°F. Different burners can be used, including forced-draft burners for smokeless combustion of heavy hydrocarbons, anti-flashback burners and low-NOx (oxides of nitrogen) burners.
THERMAL OXIDIZERS
To reach higher levels of destruction efficiency and lower emissions, we can turn to thermal oxidizers (Figure 1). Thermal oxidizers employ a wide variety of designs, but can be generally split into three main categories: DFTO; regenerative thermal oxidizers; and catalytic thermal oxidizers. The main difference between a thermal oxidizer system and a combustor is that a thermal oxidizer does not rely on directly igniting the process gas for oxidation. A thermal oxidizer sustains the proper conditions for oxidization of the combustible materials present in the process gas by maintaining an operating temperature sufficiently above the auto-ignition point by providing enough time for combustion and by the presence of excess oxygen to complete the oxidation reactions (Figure 2).
FIGURE 1. These steam-generating thermal oxidizers with waste-heat boilers represent an example of an enclosed combustion technology being used for emissions control in a degassing system that ultimately generates inert gases
FIGURE 2. Thermal oxidizers are differentiated from conventional combustors because they use excess oxygen to complete oxidation reactions at a suitably high temperature
DIRECT-FIRED THERMAL OXIDIZERS
A DFTO operates through the use of a burner to heat up the chamber to proper oxidation temperatures for the required destruction efficiency. The chamber must be designed to maintain an adequate residence time and provide sufficient velocity for turbulent mixing. If the process gas has sufficient heat content, it can be used as the fuel gas for the burner. Otherwise, supplemental fuel is required to maintain the combustion temperature.
A recuperative thermal oxidizer is a variation of a direct thermal oxidizer that incorporates heat recovery into the design. Heat recovery may be achieved through a heat exchanger on a hot-oil heater, a boiler or steam superheater, or may be used to pre-heat the process gas to increase fuel efficiency. DFTO offer high destruction efficiencies of up to 99.99% and can provide lower emissions of NOx and CO.
REGENERATIVE THERMAL OXIDIZERS
A regenerative thermal oxidizer (Figure 3) operates on slightly different principles. This type of system is used for applications where the combustible concentration is below 3% of the lower explosivity limit. A regenerative thermal oxidizer employs ceramic media to capture heat from oxidation to reach thermal efficiencies of up to 98%. Thermal energy is retained by the ceramic media and is then used to heat and oxidize the process gas as it enters the thermal oxidizer. To accomplish this, the system uses multiple beds and alternates the inlet and outlet of the oxidation chamber. A two-bed system would cycle approximately every two minutes, allowing heat to be captured by the ceramic media on the outlet and heating the process gas from residual heat in the inlet bed. Once the system cycles, the direction of flow is reversed, allowing the temperature to be regenerated on the beds. Through this process, a regenerative thermal oxidizer can operate on little to no fuel and achieve 98.5% destruction efficiency and low NOx and CO emissions, even with extremely lean process gases (gas that contains few or no liquefiable liquid hydrocarbons and is not able to combust on its own, usually requiring additional outside fuel to initiate combustion). The addition of a purge step to the cycle requires at least one additional bed, but increases destruction efficiency up to 99.5% by ensuring that any process gas that is present partway through a bed during a cycle transition is completely oxidized.
FIGURE 3. Regenerative thermal oxidizers capture the heat from oxidation, which is retained by a ceramic media and is then used to heat and oxidize the process gas
CATALYTIC THERMAL OXIDIZERS
A catalytic thermal oxidizer is another type of thermal oxidizer that is used when high fuel efficiency is required. This type of oxidizer utilizes a catalytic bed to promote oxidation, lowering the temperature required to oxidize the process gas. Because of the lower temperature, a catalytic thermal oxidizer uses less fuel than a DFTO and can even be designed to be self-sustaining through the use of a heat exchanger to pre-heat the process gas. This type of system is limited by the combustible concentration of the process gas and is limited to components that will not poison the catalyst. For the correct applications, a catalytic thermal oxidizer can offer high destruction efficiency and low NOx and CO emissions.
A new class of advanced combustor called the certified ultra-low emissions burner can achieve high destruction efficiencies and extremely low NOx and CO emissions. This type of combustor has been used in environmentally sensitive areas to achieve best-available control technology (BACT) emissions levels. These devices use surface pre-mix combustion to create short-lived, low-temperature flames that are extremely efficient. This reduces flame temperature, resulting in low NOx, but also can provide destruction efficiency of up to 99.99%.
SELECTION GUIDANCE
When selecting a combustion system, emissions and destruction efficiency have become the primary criteria. Across the industry, there is pressure, and sometimes economic incentives as well, to reduce NOx and CO emissions, along with emissions of volatile organic compounds (VOCs). With this in mind, the first step should be to determine what local emissions guidelines apply to the specific device, and to evaluate the benefits in reducing emissions. There are several cutoff points to be aware of. A simple enclosed combustor will achieve about 98% destruction efficiency. This can be achieved by almost any diffuse flame burner without any additional effort. Up to 99.5% destruction efficiency can be achieved with a temperature-controlled combustor, a regenerative thermal oxidizer or a catalytic thermal oxidizer. Above that, a DFTO or an ultra-low-emissions combustor is required. Although the difference between 99.5% and 99.9% destruction efficiency may seem small, half a percent improvement on destruction efficiency represents five times greater emissions for the former compared to the latter.
NOx emissions.NOx emissions have traditionally been especially hard to control. NOx is formed through various mechanisms during combustion, which, if not addressed, can create large amounts of this pollutant. A diffuse flame burner will generate the largest amount of NOx, so typically any enclosed combustor, even temperature-controlled models, will produce relatively large amounts of NOx. This includes DFTO, which, even though they offer great destruction efficiency, do not greatly improve over simpler combustors in NOx generation. There are several low-NOx burners and designs that can improve NOx emissions for combustors and DFTO. Other solutions are also available, such as ammonia injection, but that can prove to be quite expensive. Regenerative and catalytic thermal oxidizers can offer low-NOx emissions.
Fuel efficiency.Fuel efficiency is another important, yet frequently overlooked, consideration for selecting an enclosed combustion system. Where a fuel source, such as natural gas, is inexpensive, it is not always feasible to invest in a higher-cost system to increase fuel efficiency, but many products are still worth considering. Regenerative thermal oxidizers offer the greatest fuel efficiencies, recovering up to 98% of thermal energy. These systems are ideal for low-concentration and high-flowrate applications. Catalytic thermal oxidizers can also operate at high thermal efficiencies by incorporating heat exchangers to pre-heat the process gas before it passes through the catalyst. Finally, a recuperative thermal oxidizer can be used to pre-heat process gas to increase fuel efficiency, or it can be used to recover heat to use in another process in the plant. This can put the thermal energy generated by the thermal oxidizer to use in generating steam or other cost-saving applications.
Handling challenging components. Other product-selection decisions revolve around the type of process gas being handled. Corrosive components, such as hydrogen sulfide and halogenated compounds, demand systems capable of safely disposing of these components. Typically, once the concentration of any of these compounds reaches a certain level, the safest and most effective way of destroying them is through specially designed DFTO. Other combustion systems are either sensitive to the presence of these chemicals, such as catalytic thermal oxidizers and regenerative thermal oxidizers, or they are not suitable for handling more dangerous chemicals, such as with enclosed flares and combustors. DFTO must be designed to handle these chemicals, especially in the selection of the refractory media. For hydrogen sulfide, a ceramic-fiber blanket can be used, but the oxidizer should employ a hot-shell design to prevent acid gas condensation. For this design, a wind shield is installed outside of the oxidizer shell to prevent wind or rain from cooling the surface of the chamber. This prevents the sulfur dioxide and sulfur trioxide that is produced by the combustion process from condensing into sulfurous and sulfuric acids. For halogenated compounds, a high-grade refractory media that is high in alumina and can withstand the corrosive products of combustion must be used
With all the different factors that can influence the selection of an enclosed combustion system, it can be difficult to determine where to start. In general, the decision factors should prioritize process-gas composition, followed by emissions, and finally fuel efficiency and capital costs. Following these priorities ensures that the equipment selected provides the required performance at the least capital and operational costs. Proper selection requires that these factors be researched and determined in advance to ensure that the expectations for the equipment are in line with the operational requirements. Armed with this information, the descriptions in this article can provide a starting point for equipment selection to ensure that the final decision achieves the requirements for the application.
This article originally appearing on Chemical Engineering Online: https://www.chemengonline.com/enclosed-combustion-equipment-technology/?printmode=1
AUTHOR
Anu D. Vij is chief operating officer (COO) of Ship & Shore Environmental Inc. (2474 N. Palm Drive, Signal Hill, CA 90755; Phone: +1(562) 997-0233; Website: www.shipandshore.com). Vij has over twenty years of experience in the environmental, chemical, petrochemical and air-pollution-control industries, and has specific expertise in thermal oxidation technologies. As COO at Ship & Shore, he oversees several business units, including Sales, Finance, Engineering, Project Management, Procurement, Production and Services. Prior to joining Ship & Shore, Vij served as vice president, enclosed combustion systems at Aereon and was director of engineering at OnQuest Inc. Vij holds a M.S.Ch.E. from the University of Southern California and a B.S.Ch.E. from Panjab University in India.
Categorised in: Air pollution, California, EPA, Industry news, Media, News, News, RTO