Direct Fired Thermal Oxidizers
What is a DFTO?
A Direct Fired Thermal Oxidizer (DFTO) is an industrial air pollution control system that destroys volatile organic compounds (VOCs) and hazardous air pollutants (HAPs) from the environment. The DFTO heats the polluted air to a high temperature with an excess amount of air, causing the pollutants to oxidize and break down into non-hazardous compounds, such as water vapor and carbon dioxide.
Since 1950, DFTOs have been used extensively in manufacturing industries to abate VOCs and HAPs. Initially, this clean air technology was used specifically for the plastic manufacturing industry. It quickly became more popular among other industries as well such as paint and coating, chemicals, flexographic printing and packaging food, pharmaceuticals, and much more. Over the years, DFTOs have undergone many updates and enhancements such as improved combustion control systems, better heat recovery technologies, and more efficient designs.
How it Works in a Glance:
The DFTO brings a burner near hazardous gases and provides enough residence time to achieve the desired destruction removal efficiency (DRE) of the VOCs. A DFTO typically works between temperatures of 1,500°F (815°C) and 2,000 °F (1,100°C).
How it Works Technically:
The DFTO works with high temperatures as a result of combustion to convert the HAPs & VOCs gases into non-harmful gases. This process technically works in the following steps:
- Contaminated air is drawn into the DFTO, typically through an inlet duct passing through filtration, fluid removal systems where needed, flame or detonation arrestors if LEL is higher than 50%.
- Inside the DFTO, polluted air is combusted and 99% or higher of the VOCs are destroyed and converted into carbon dioxide and water.
- The resulting clean gases are then exhausted from the DFTO through a stack.
- The hot exhaust gases can also be used to generate steam, hot oil, or hot process air for ovens by means of a waste heat boiler, hot oil heater, or air-to-air heat exchanger. The heat generated can also be repurposed into steam production, heating, or electricity generation.
- Exhaust gases contain much high temperature energy that can be used to preheat cooler inlet process air through a heat exchanger which will reduce fuel consumption and burner size (Recuperative Thermal Oxidizer).
- Finally, the cooled, clean air is routed into the atmosphere through the outlet switch values.
The Advantages of Using a Ship & Shore DFTO at Your Facility:
- Ship & Shore DFTOs are custom designed for the highest reliability
- Ship & Shore engineers have years of experience and are very knowledgeable about all processes with a wide range of engineering backgrounds and capabilities
- Cost effective
- Suitable for various industries reduces harmful gases up to 99%+
- Compact in size in comparison to other air pollution control system options
- Reduces co2 and enhances energy efficiency
- Capable of absorbing heat rapidly
- Low maintenance
- Safe and easy to use with remote capabilities
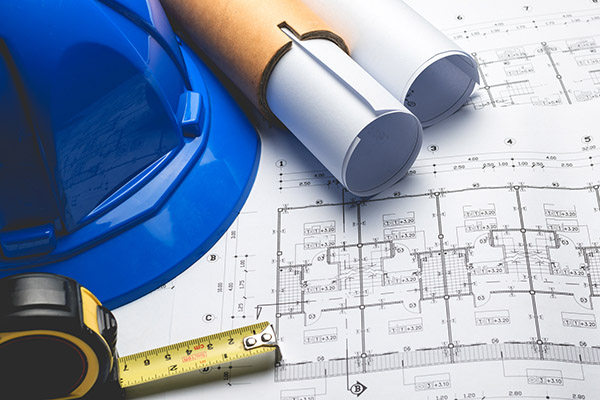