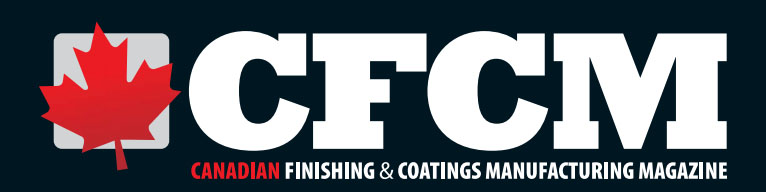
CFCM – Canadian Finishing & Coatings Manufacturing Magazine: Cutting the Costs of Pollution Control
November 8, 2018 12:18 pmCFCM - Canadian Finishing & Coatings Manufacturing Magazine: Cutting the Costs of Pollution Control
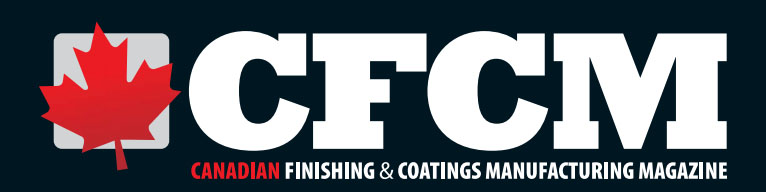
This article originally appeared in CFCM, Canadian Finishing & Coatings Manufacturing Magazine, Nov/Dec 2018
Cutting the Costs of Pollution Control
Nobody likes spending money on pollution control equipment. The perception is that it only adds to costs, not productivity, and there are few thanks for companies that install it.
“We make the equipment nobody wants to buy,” concedes Jim Kuzara, technical sales manager with Ship & Shore Environmental. “VOC abatement technology is our primary field of activity and it is a necessary requirement to do business in today’s environmentally sensitive economy.”
The company’s various thermal oxidizer designs do not only combust volatiles, but can also be used to create heat exchange, or even to generate steam. Kuzara remarks that this can cut a plant’s energy usage, defying the general assumption that there is no cost benefit from emission reduction.
“Our competitors have tended to be more transient than us,” he says. “We have been in the industry with this sort of technology for almost 20 years now. We’re not the largest manufacturer of this type of equipment, but we are in the middle of the field.”
One of the company’s strengths, he says, is being very process-oriented. Where other suppliers simply provide a standard thermal oxidizer system, Ship & Shore tries to understand the customer’s process before completing a sale.
One of the more common systems it builds is the Regenerative Thermal Oxidizer. In these systems, a fan supplies air from the process to the RTO. There are two heat exchanger beds in the system, with a burner and combination chamber between them.
“The RTO is ideal because it provides up to 99 percent destruction efficiency, but it’s also thermally efficient,” Kuzara says. “We can recover up to 97 percent of the energy in the system.”
In such a system, a fan pushes the air through an inlet manifold, which directs the air up into one of the two heat exchanger chambers, which have ceramic beds. The incoming air is pre-heated to between 900 and 1000 deg F prior to entering the combustion chamber (gas then heated up to 1500 deg F). Exhaust gas from the combustion chamber is then directed through a second ceramic heat exchange bed where heat is stripped from the exhaust. The resulting clean process air is released to atmosphere as carbon-dioxide and water vapor.
As the initial ceramic heat exchanger starts to cool, the second ceramic heat exchanger gains heat. At this point in the process, the incoming process exhaust is reversed – process air directed to the second ceramic bed which is newly heated. The incoming stream is now pre-heated by the second bed, moves into the combustion chamber, and then to ceramic bed number 1 where heat is now stripped from the exhaust leg of the system and then to atmosphere.
“We reverse the chamber every two minutes or so to maintain this heat balance,” Kuzara explains. “This is all automatic, and can stat and shut down at the end of the day automatically. It is well insulated to stay as efficient as possible, and for safety reasons.”
In an ideal world, the move to more water-based systems would have pushed solvent-based coatings out of the market. However, no every water-based formulation has worked as advertised, and solvents will still be widespread for the foreseeable future.
“At the end of the day there is often a requirement that you need this type of equipment,” he continues. “We might have to configure for a specific load of VOC. If there is enough solvent, perhaps three to four percent of the lower explosive limit air-stream, there is sufficient BTU value where you can basically turn off the gas, it becomes self-sufficient – little or no supplemental fuel is required.”
There are various units installed by Ship & Shore in Canada, Montreal and Vancouver being particularly strong markets. The printing industry is a good customer, and the coil coatings business can produce a lot of effluent when it uses organic coatings. In the liquid paint field, it’s also possible to re-use cleaned-up air from burn-off systems on large paint lines.
“Our biggest customer base is existing customers,” Kuzara says. “Sometimes, we deal our own used equipment, so we can offer a used system ASAP. We have chemical engineers on staff, and we have 24/7 response on equipment problems that arise.
“As the sales person, it is my responsibility to present value added services to my customers. Whether that’s providing energy recovery, source ductwork collection systems, assisting with environmental permitting, or looking into rebate incentives. We want to be the company looking out for the customer.”
Categorised in: Air pollution, Industry news, Media, News, News, Ship & Shore, Technology, VOC Abatement