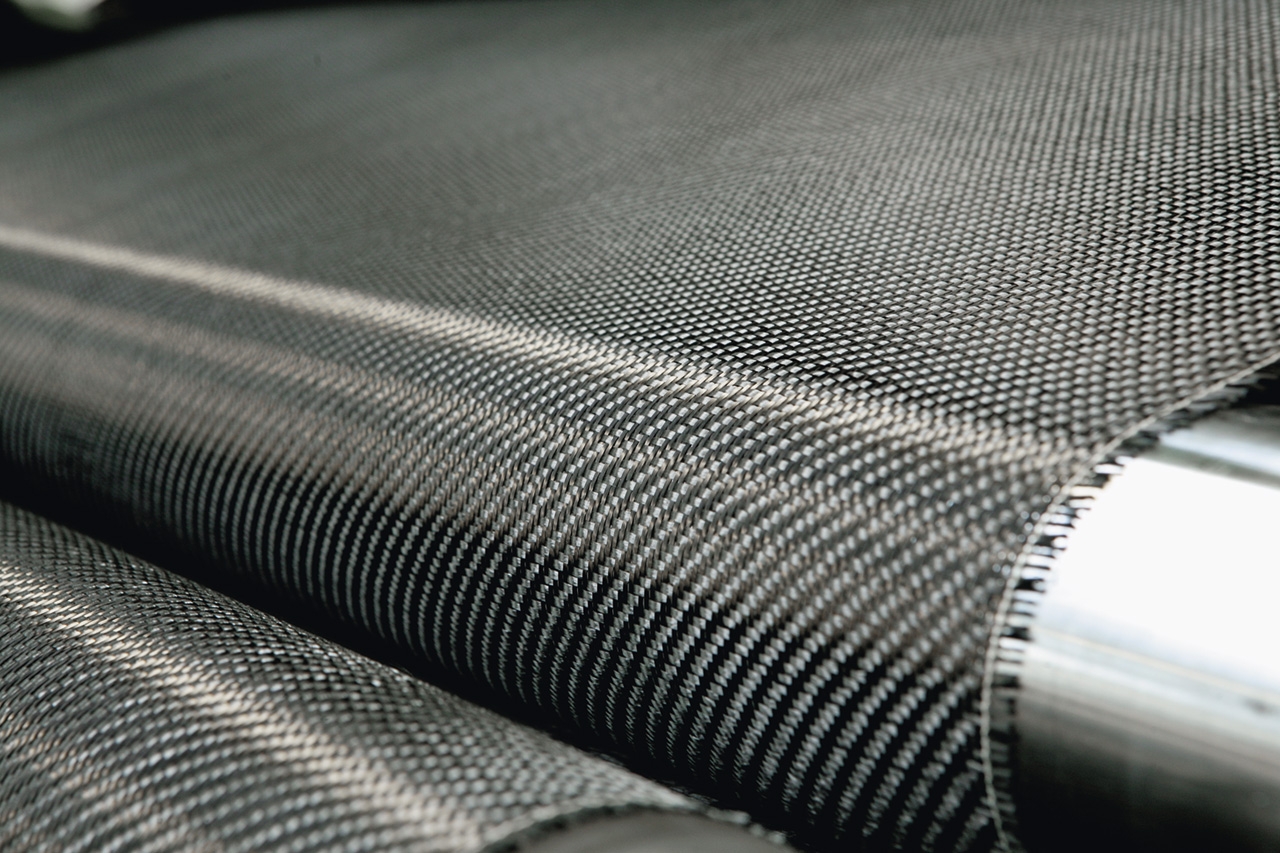
Clean Tech Solutions for Styrene Emission Abatement
July 13, 2016 10:20 amClean Tech Solutions for Styrene Emission Abatement
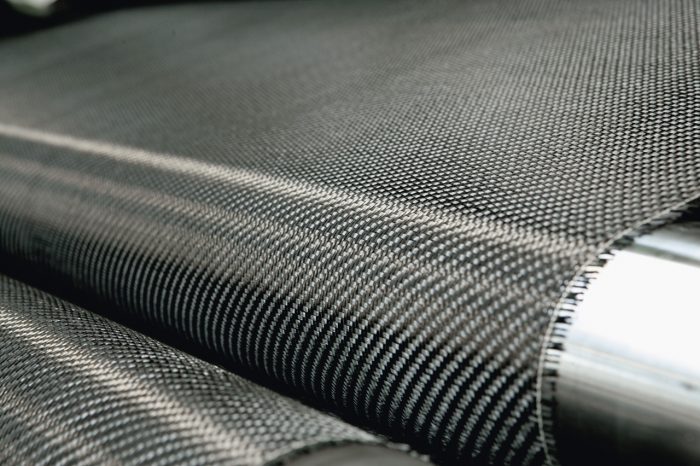
Most fiber reinforced plastics (FRP) processors are major sources of volatile emissions. The emissions from FRP processing facilities include styrene, the volatile component of polyester resin and gelcoat; and acetone, a solvent used to clean tools and other surfaces contaminated with resin.
Ship & Shore is major supplier of emissions-control systems and offer consulting and options to first see if they can change material formulations and maintain quality without adding equipment, but also designs, manufacturers and installs Thermal Oxidizers and Regenerative Thermal Oxidizers for styrene emission abatement equipment for the FRP Industry to control odor and meet stringent zoning and compliance regulations.
CLEAN TECH SOLUTIONS FOR STYRENE EMISSION & ODOR ABATEMENT
Regenerative Thermal Oxidizers (RTOs)
Among the equipment options are thermal oxidizers—air pollution and odor contol systems that burn off VOC emissions at 1200 F. A more energy-efficient alternative is a regenerative thermal oxidizer, or RTO, which is a thermal oxidizer that uses ceramic media as a heat exchanger for recovery of combustion heat energy. A third option includes a fume concentrator and an RTO. This two-stage emissions-control system first concentrates the styrene fumes on adsorptive media and then destroys the VOCs in a small oxidizer. The concentrator/RTO system is capital intensive, but its operating costs are lower than those of oxidizers or RTOs alone because the concentrated VOCs make the unit “self-fueling.”
S&SE RTOs are designed to meet all compliance regulations and significantly reduce energy consumption and operating costs by re-using and re-directing thermal energy that is generated during the manufacturing process. Regenerative thermal oxidizers are highly effective for air pollution compliance and odor abatement of styrene emissions.
Permanent Total Enclosures (PTEs)
Permanent Total Enclosures (PTEs) are a highly effective way to prevent fugitive styrene emissions from entering the atmosphere. By completely surrounding the emission source, the process emissions from the EPS Molding Process can be minimized and concentrated for more cost effective destruction in a VOC control device.
Heat Recovery for FRP Industry Process
Installation of economizer in stack will reduce exhaust temperature to 300°F. Additionally installing feedwater make-up heat exchanger in continuous blowdown discharge (saves cooling water) as well as a combustion air pre-heater in exhaust stack. This typically adds approximately 4% to overall efficiency.
Ship & Shore provides engineering and air pollution and odor abatement equipment globally. To learn more about our approach on Styrene Emissions for the FRP Industry please contact one of our regional experts by EMAIL or call(562)997-0233
Categorised in: Air pollution, Energy, EPA, News, News, Technical