Catalytic Oxidizers
What is a Catalytic Oxidizer and How Does it Work?
A catalytic oxidizer is an air pollution control system that destroys volatile organic compounds (VOCs) into primarily carbon dioxide and water. It is similar to a Direct Fired Thermal Oxidizer (DFTO) except that a catalytic oxidizer utilizes a metal catalyst to lower the reaction temperature to oxidize the VOCs into harmless gases. A catalyst is a substance that accelerates the rate of a chemical reaction at a lower temperature and is not to be a part of that reaction. Typically, the destruction rate of a catalytic oxidizer is 96% or higher where required.
Process gases containing VOCs are directed through a heating chamber where these gases are heated to an increased temperature with use of a burner. The heated gases pass through the catalyst bed, which could be a series of blocks in the form of a wall or pellets, at a certain depth in metal baskets.
The catalyst can be of a noble metal supported type such as platinum, rhodium, or stainless steel. It can also be a ceramic substrate or a metal oxidize based type.
Since the reaction “combustion” takes place in the catalyst bed, the exhaust after the catalyst has been raised in temperature so an air-to-air heat exchanger can be installed to raise the incoming process temperature, resulting in fuel savings because a smaller burner is used.
Process emissions are passed through a filtration system where it is required and through a heat exchanger where it is used, before entering the combustion chamber. In the combustion chamber, process fumes are heated to the required temperature before passing through the catalyst beds. Exhaust from the catalyst bed passes through the heat exchanger and heats the incoming process fumes before they enter the stack and cleaner exhaust and air is released into the atmosphere.
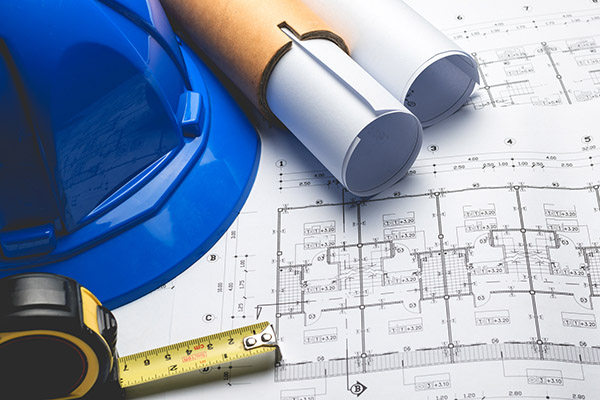