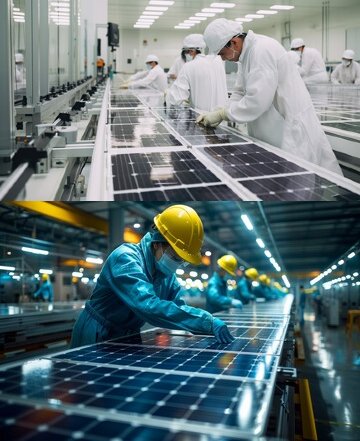
#TechTalk | Solar Panel Production – Solvent Emissions Concerns
January 22, 2025 8:37 am#TechTalk | Solar Panel Production - Solvent Emissions Concerns
Solar energy has emerged as a frontrunner in the renewable energy race, driven by growing sustainability and environmental awareness.
However, as with any new technology, its ecological impact raises important questions. Is solar energy genuinely ‘green,’ or are there hidden environmental impacts realized?
Over the last decade, the solar industry has grown rapidly. Solar panels, while beneficial for renewable energy production, have concerns associated with their production.
Solar panels depend on substances like silicon, silver, and rare earth elements. The manufacturing of solar panels utilizes dangerous chemicals such as cadmium, lead, and arsenic. Inadequate management and disposal of production substances may result in environmental pollution and pose health hazards to workers and the general population.
PV Module Manufacturing
From the Office of Energy Efficiency & Renewable Energy / US Dept of Energy
Silicon Photovoltaic Panel Construction
In general, most commercially available PV modules rely on crystalline silicon as the energy absorbing material. These modules have several manufacturing steps that typically occur separately from each other.
Base Material Polysilicon Production – Polysilicon is a high-purity, fine-grained crystalline silicon (sand) product, typically in the shape of rods or beads depending on the method of production. Polysilicon is commonly manufactured using methods that rely on highly reactive gases, synthesized primarily using metallurgical-grade silicon (obtained from quartz sand), hydrogen, and chlorine.
Ingot and Wafer Production – To turn polysilicon into wafers, polysilicon is placed into a container that is heated until the polysilicon forms a liquid mass. Silicon ingots are formed and then sliced into very thin wafers for panel bundling.
Cell Fabrication – Silicon wafers are then fabricated into photovoltaic cells. The first step is chemical texturing of the wafer surface, which removes saw damage and increases how much light gets into the wafer when it is exposed to sunlight. The subsequent processes vary significantly depending on device architecture. Most cell types require the wafer to be exposed to a gas containing an electrically active dopant and coating the surfaces of the wafer with layers that improve the performance of the cell. Screen printing of silver metallization for electrical contacts is also very common among cell types.
Module Assembly – At a module assembly facility, copper ribbons plated with solder connect the silver busbars on the front surface of one cell to the rear surface of an adjacent cell in a process known as tabbing and stringing. The interconnected set of cells is arranged face-down on a sheet of glass covered with a sheet of polymer encapsulant. A second sheet of encapsulant is placed on top of the face-down cells, followed by a tough polymer backsheet or another piece of glass. The whole stack of materials is laminated in an oven to make the module waterproof, then fitted with an aluminum frame, edge sealant, and a junction box (some PV panel rework possibly needed).
In the module assembly process bonding of multiple layers of glass, film, foils, with solvent based adhesives is performed.
The entire process results in emissions containing EB acetate, butyl glycol acetate, ethanol, alcohols, methanol, esters, among other Volatile Organic Compounds (VOCs) and possible Hazardous Air Pollutants (HAPs) components. Chemicals strictly regulated by the US EPA and State regulatory Authorities.
Volatile Organic Compounds (VOCs)
Organic chemical compounds that have high enough vapor pressures under normal conditions to significantly vaporize & enter the atmosphere. IMPORTANCE – Under sunlight, VOCs react with nitrogen oxides emitted from industrial activities to form ozone / smog which is bad for us and the climate.
In addition, Hazardous Air Pollutants (HAPs) are Chemicals known or suspected to cause cancer or to have other serious health effects, such as respiratory, reproductive or birth defects, and create adverse environmental impact.
Based on very high recent production growth, tons of these emissions have found their way into the atmosphere. As emissions grow, tonnage limits established by Federal law are triggered, requiring add-on air pollution control equipment to minimize VOC/HAP emissions to the atmosphere. Typically, a Regenerative Thermal Oxidizer (RTO) is utilized to combust pollutants to 99% destruction efficiency with very high thermal efficiencies (up to 97% energy recovered from the abatement process). RTO technology minimizes capital cost investment while providing the most energy efficient operating platform.
Over the last few years, Ship & Shore Environmental has built RTO VOC control systems for many prominent Solar PV Panel manufacturers in the United States. We welcome the opportunity to share our experience from the industry.
Contact sales@shipandshore.com or call +1(562) 997-0233 to learn more.
Categorised in: Industry news, News, News, Ship & Shore, TechTalk