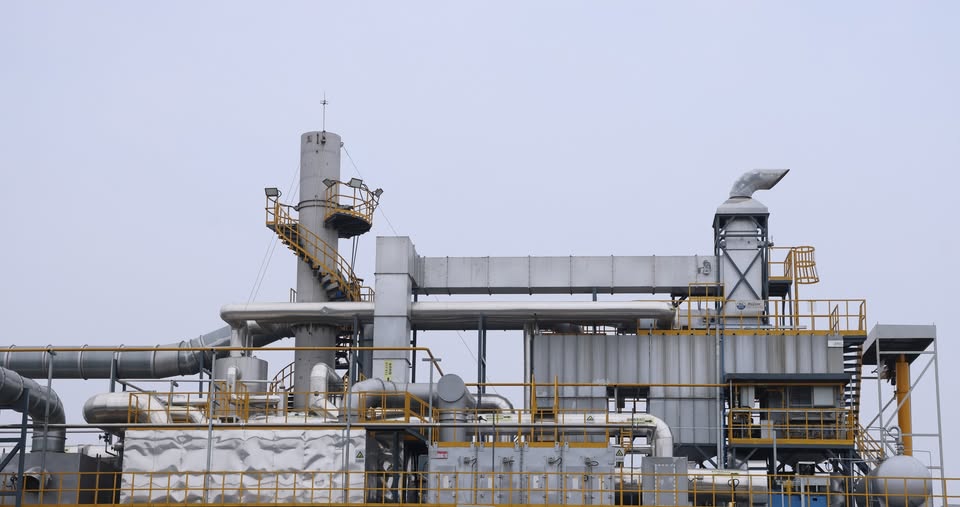
#TechTalk – Semiconductor Manufacturing: Manages Emissions from Etching and Cleaning
January 8, 2025 8:44 am#TechTalk - Rotary Concentrator and Regenerative Thermal Oxidizer (RTO) System
Evolution of VOC Abatement Technologies
Traditional methods like scrubbers or direct incineration were inefficient for low-concentration VOC streams. The rotary concentrator and thermal oxidizer system provide an energy-efficient, scalable solution that is now the standard for emission control.
Rotary Concentrator
Function
The rotary concentrator optimizes the RTO by concentrating low-concentration VOCs, improving performance and cost-efficiency.
Key Components
- Rotating Wheel: Made of zeolite or activated carbon, it adsorbs VOCs.
- Segregated Sections:
- Adsorption Zone: Low-VOC air is passed through and adsorbed onto the wheel.
- Desorption Zone: Heated air desorbs VOCs.
- Cooling Zone: Regenerates the wheel.
- Pre-Filtration: HEPA filters or mist eliminators remove particulates, prolonging media life.
Operational Parameters
- Adsorption Temperature: 20°C–40°C
- Desorption Temperature: 180°C–250°C
- Airflow Rates: 1,000 to 100,000 SCFM.
Removal Efficiency
Achieves VOC concentration ratios of 10:1 to 20:1, improving RTO efficiency.
________________________________________
Regenerative Thermal Oxidizer (RTO)
Function
The RTO destroys VOCs and HAPs via high-temperature oxidation, converting them to CO₂ and H₂O.
Key Components
- Heat Exchangers: Ceramic media recover heat, with up to 97% efficiency.
- Burner: Maintains high temperatures (1,400°F–1,600°F).
- Chambers and Valves: Ensure optimal heating and cooling.
Process Flow
- Concentrated air enters the RTO.
- Air passes through ceramic media for preheating.
- VOCs are oxidized in the combustion chamber.
- Clean air exits, transferring heat to incoming air.
Removal Efficiency
Achieves up to 98% VOC destruction efficiency.
Benefits
- High Destruction Efficiency: Meets the strictest regulations.
- Energy Savings: Through heat recovery.
- Robust Design: Ensures long-term operation.
________________________________________
Combined System Advantages
Synergy
- Cost Efficiency: Reduced air volume lowers fuel consumption.
- Compact Design: Smaller RTOs due to reduced flow rates.
- High Performance: Meets regulatory requirements.
Quantitative Analysis
- A 10:1 concentration ratio reduces fuel costs by up to 70%.
- Energy savings reduce carbon emissions.
Applications
- Paint and Coating: Controls overspray and curing VOCs.
- Semiconductor Manufacturing: Manages emissions from etching and cleaning.
- Printing: Reduces VOCs from ink drying.
- Chemical Processing: Controls off-gases from reactors.
________________________________________
Maintenance and Operational Considerations
Rotary Concentrator
- Inspection: Check the wheel for wear.
- Cleaning: Ensure efficiency.
- Filter Monitoring: Clean or replace pre-filters.
RTO
- Ceramic Media: Inspect for damage.
- Burner Calibration: Ensure combustion efficiency.
- Valve Inspections: Prevent leakage.
Predictive Maintenance
IoT-based monitoring minimizes downtime and costs.
Categorised in: Industry news, News, News, Ship & Shore, TechTalk