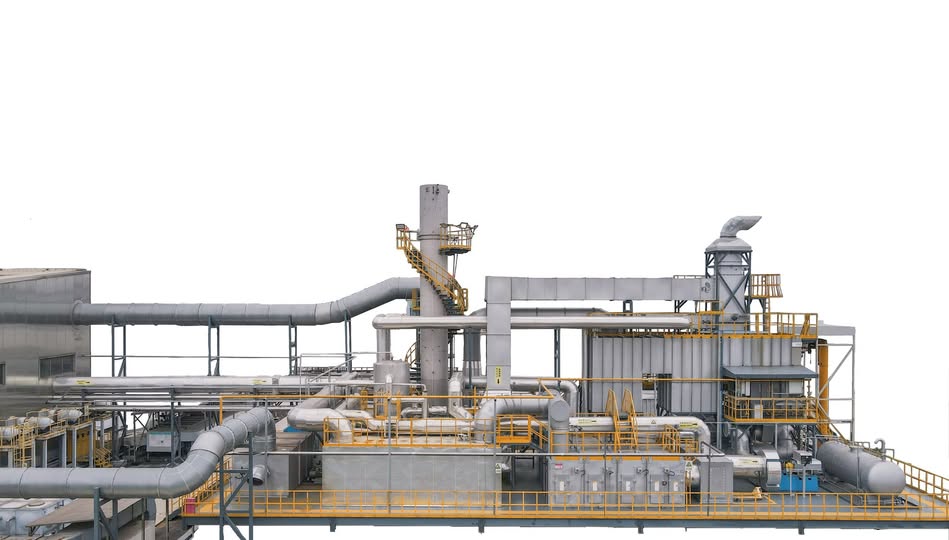
#TechTalk – How the Zeolite Concentrator Bundle with RTO (Regenerative Thermal Oxidizer) Drives Innovation in Semiconductor Applications
January 15, 2025 7:53 am#TechTalk - How the Zeolite Concentrator Bundle with RTO (Regenerative Thermal Oxidizer) Drives Innovation in Semiconductor Applications
A zeolite concentrator bundled with a Regenerative Thermal Oxidizer (RTO) is an integrated system designed to reduce volatile organic compound (VOC) emissions from industrial processes. This system efficiently handles large volumes of low-concentration VOC-laden air while minimizing energy consumption. Here’s how it works:
1. Zeolite Concentrator (VOC Concentration Step):
Function: The zeolite concentrator is a rotating system that adsorbs VOCs from a large volume of air and concentrates them into a smaller airflow, increasing their concentration for easier destruction in the RTO.
Structure:
Rotor or Wheel: The zeolite concentrator features a honeycomb structure coated with zeolite, a porous material that adsorbs organic compounds.
Zones: The wheel is divided into three zones:
Adsorption Zone: VOC-laden air passes through, and the zeolite adsorbs VOCs.
Desorption Zone: A smaller, hot air stream desorbs the VOCs, regenerating the zeolite.
Cooling Zone: The zeolite is cooled before returning to the adsorption zone.
Result: This process reduces the air volume entering the RTO while concentrating the VOCs for more efficient destruction.
2. Regenerative Thermal Oxidizer (RTO) (VOC Destruction Step):
Function: The RTO destroys concentrated VOCs through thermal oxidation, converting them into harmless byproducts such as CO₂ and H₂O.
Structure:
Ceramic Heat Exchangers: The RTO contains chambers filled with ceramic media to store and transfer heat.
Burner: Provides additional heat if needed to maintain the oxidation temperature (typically 760-820°C).
Operation:
Pre-heated air enters the combustion chamber from the ceramic media.
VOCs are oxidized at high temperatures.
Clean, hot exhaust passes through another ceramic bed, transferring heat to incoming air.
Result:
The RTO operates efficiently, using minimal fuel due to its regenerative heat recovery design.
Combined Operation:
Low Energy Consumption: The zeolite concentrator reduces the air volume entering the RTO, improving its efficiency by processing a smaller, concentrated stream.
High Destruction Efficiency: The RTO ensures near-complete destruction of VOCs, achieving destruction efficiency of up to 99%.
Scalability: This system is ideal for high-flow, low-VOC facilities like automotive paint booths, chemical plants, or semiconductor manufacturing.
Advantages:
Cost-Effective: Reduced operational costs due to lower air volume and energy-efficient design.
Compact Footprint: The zeolite concentrator minimizes the need for larger oxidizer systems.
Environmental Compliance: Helps meet stringent air pollution regulations.
By combining the zeolite concentrator with an RTO, facilities can efficiently handle VOC emissions, reduce environmental impact, and optimize energy use.
Contact sales@shipandshore.com or call +1(562) 997-0233 to learn more.
Categorised in: Industry news, News, News, Ship & Shore, TechTalk