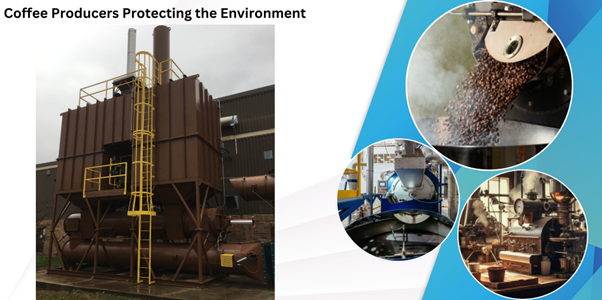
#TechTalk – Coffee Producers Protecting the Environment
February 12, 2025 9:31 am#TechTalk - Coffee Producers Protecting the Environment
Who does not enjoy a nice warm eye-opening cup of coffee to get the day started, or to deliver a jolt of energy during the day, or to finish off a nice meal? Coffee is consumed all over the world and is prepared in numerous ways to the enjoyment of the masses.
Did you know that coffee preparation impacts the environment? Coffee roasting is a crucial process in the coffee industry. Whether you are a super-sized conglomerate producer or side street boutique brewer transforming raw green beans into aromatic brown beans, the roasting process generates various pollutants that need to be addressed to minimize environmental impact and comply with State and Federal air quality regulations.
Coffee Emissions
- Particulate Matter – Fine particles of coffee chaff (opacity)
- Volatile Organic Compounds (VOCs) – Organic Chemicals that easily vaporize at room temperature and contribute to health affecting smog. Aldehydes, Keytones, Pyrazines, Furans, Phenolics, Pyrroles, etc.
- Nitrogen Oxides (NOx) – Chemical combining with VOCs to create smog.
- Carbon Monoxide (CO) – A product of incomplete combustion.
- Odors – Strong aromatics that can be a nuisance to the local area
A great focus is placed on the roasting operation of the coffee process. But bean cooling also generates large volumes of air that need to be treated. Both roasting and cooling of the beans creates off gases and chaff particulates that need to be dealt with. The US EPA has put in place limitations on the number of pollutants that can be emitted by an operation. These limits can vary based on plant location and air attainment status. Please consult the US EPA to determine specific limits.
How to treat emissions:
Particulates (chaff from beans) can be filtered in a variety of ways. Filtration is typically required to remove particulate matter from the air for improved air quality, but more importantly to protect downstream operation of chemical emission destruction devices (devices that might get fouled and affect operation).
- Static high temperature baghouse type filters or mechanical filters can effectively be used (generally lower cost). These can be set up to self-clean, replace, or manually clean on a periodic basis.
- Electrostatic precipitators (ESP) are generally more elaborate and more expense to supply and operate but are more effective in high production type removal operations. They’re typically very large, self-cleaning, and consume large amounts of electricity in operation.
Unfortunately, filtration does not address the chemical emission portion of the coffee roasting process. Other equipment is needed to treat VOC, CO, and Odors. Thermal oxidizer equipment operates at high temperatures to combust pollutants via natural gas burners (generally at about 1500 degrees F). Thermal oxidizers are commonly used within the coffee industry. It is commonly recommended to use filtration technology upfront of any oxidizer technology.
Thermal Oxidizers include Direct Fired Thermal Oxidizers, Recuperative Thermal Oxidizers, and Regenerative Thermal Oxidizers (RTOs).
- DFTOs have a very high destruction efficiency, are particulate tolerant, but consume a very large amount of natural gas in their operation. Typically implemented with small air volume highly concentrated chemical air streams.
- Recuperative Thermal Oxidizers have very high destruction efficiency, moderate cost to operate, may need cleaning over time, but recovers approximately 50% of the combustion energy via heat exchangers in its operation. Typically used with small to medium chemical air streams with low to moderate chemical concentrations.
- RTO technology has very high destruction efficiency (up to 99%) and is used typically with higher exhaust volumes. RTO operation is very well suited for higher production operations that have large exhaust volumes of roasting and cooling air, with small to moderate chemical concentrations. Thermal efficiency of an RTO is in the 95 to 97% range for very low cost of operation / natural gas use.
Catalytic Oxidizers can also be used for their lower temperature operation and high destruction efficiency but unfortunately the technology is subject to catalyst masking from particulate breakthrough. Particulate migration into the catalyst would reduce destruction performance and would require costly cleaning or replacement of the catalyst. The other combustion technologies are reasonably tolerant of particulate break-thru or can be self-clean from organic materials.
Scrubber technology can also be used to treat both particulate and chemical emissions, but they typically do not meet the higher efficiencies that thermal oxidizer technology provides. They also have their own secondary water treatment issues / water supply / conditioning needed for the operation. Scrubbers do not adequately address odor and non-water-soluble chemical constituents.
Also NOT recommended is Activated Carbon Filter technology. Due to the high temperatures of the process, emissions will likely pass through the carbon or zeolite material affecting performance. Carbon or zeolite media is also subject to particulate masking resulting in the need to clean or replace which can be costly.
Because there are challenging production conditions, variable emissions, high temperatures, moisture content, odors, space constraints, energy impacts, etc. Ship & Shore Environmental engineers can work with your coffee production team to make proper equipment recommendations to minimize capital equipment cost, operating cost, and system maintenance needs.
Contact us to design a system that best controls particulate, VOC, NOx, CO, and Odors at at service@shipandshore.com or call (562) 997-0233.
Categorised in: Industry news, News, News, Ship & Shore, TechTalk