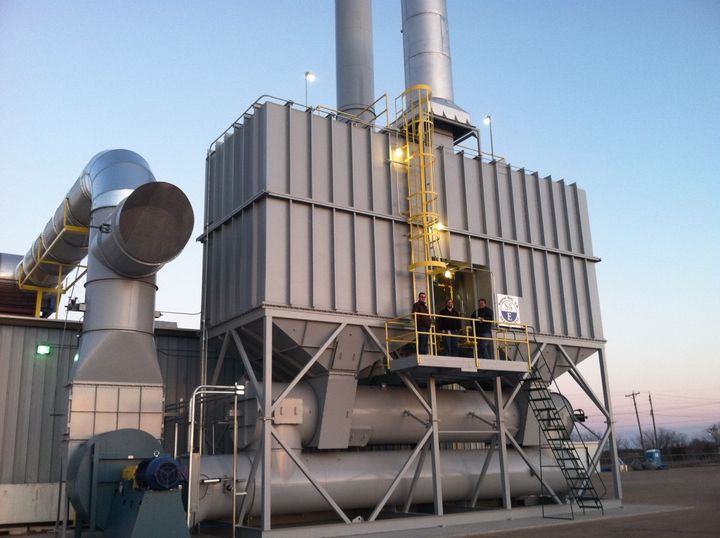
#TechTalk – Ship & Shore Environmental Cutting Emissions in the Print Industry
October 2, 2024 8:48 am#TechTalk - Ship & Shore Environmental Cutting Emissions in the Print Industry
Attractive eye-catching packaged product helps keep merchandise moving from the shelves. Multicolored, high gloss, laminations, and dimensional printing techniques all conspire to draw the consumer in for purchase. Food, pharmaceuticals, bulk packaging, paper, film, and corrugated materials all seek to gain a competitive advantage through unique and highly visible packaging.
Ink or coating materials are chosen to create the best finish effect and print durability. Typically, solvent-based or water-based coating materials are used. Although both coating types contain solvent material, water-based materials have significantly less solvent content. It is the solvent based printing operations that emit large amounts of Volatile Organic Compounds (VOCs) that are the focus of regulatory agencies and generally require abatement controls.
Why do we control these emissions?
VOC emissions that enter the atmosphere combine with nitrogen oxides and UV rays (sunlight) to form smog that has been proven to cause respiratory health problems. Other solvents have been classified as Hazardous Air Pollutants (HAPs) and have been shown to be cancer causing. And of further note, the capture and treatment of Ozone emissions from corona treatment equipment has found its way into recent permits and subsequently into abatement equipment. These emissions are also unhealthy and very corrosive to surrounding plant equipment.
The goal of any well-designed printing facility is to mitigate these emissions by implementing add on abatement controls. Typically, thermal oxidizers are used in this application. Principally Regenerative Thermal Oxidizers (RTOs) are installed to minimize the impact of coating emissions in a cost effective way.
Ship & Shore Environmental, Inc. is a leading supplier of VOC abatement equipment to the printing industry and is based out of Signal Hill, CA. Ship & Shore has complete design and build capabilities. We can assist in all aspects of equipment design, regulatory permitting, ductwork collection system design, and complete after sales service. Ship & Shore also leverages rebate incentives available through local natural gas and electric utility providers for the purchase of thermal efficient control equipment.
Solvent emissions are emitted to the atmosphere in a variety of ways from printing operations.
- Press ink application exhaust areas – Flexographic, Rotogravure, Litho, Offset, etc.
- Press Tunnel drying area exhaust
- Ink mix local to the press area
- Ink/solvent storage rooms
- Ozone emissions from corona treater adhesion promoting equipment
- General press vicinity ventilation (typically for older presses)
The decision to control VOC emissions with an RTO, whether mandated by regulation or voluntarily, comes with a price. This is usually manifested in dollars and time across your organization – Manpower, capital purchase, added energy costs, regulatory permitting challenges, and facility design changes (concrete, ductwork, piping and wiring).
As a basic service, Ship & Shore provides additional Value-Added Benefits to minimize your project’s exposure. Keys to obtaining the best project value include:
- Complete understanding of the print process to maximize abatement equipment potential.
- Minimizing air flow to the oxidizer (smaller unit purchase) while enhancing fuel to the unit (fuel via VOCs in exhaust streams) to achieve less operating cost.
- Coordinating with your environmental engineers and or consultant to achieve regulatory compliance. Assistance in filing for air quality permits.
- Researching possible secondary process heat recovery opportunities to maximize energy recovery for overall lower operating costs.
- Incorporating design provisions and anticipating future process changes.
- Knowledge, experience, and relationships to take advantage of new construction incentive rebates available through natural gas and electric utility entities. These are very lucrative returns available primarily through RTO purchases.
Your abatement system supplier must be hands on and understand the core principles of manufacturing processes. Alongside plant personnel, Ship & Shore baselines, designs, and integrates environmental control technology for leaner capital outlays and cost effective operation.
In these ways, Ship & Shore places a customer in a position of success. We focus on your abatement needs while you manage the challenging business environment. Better air quality, energy efficiency, maximum profitability – Ship & Shore partners with the printing world to grow and expand businesses through the addition of well conceived environmental controls.
Categorised in: Industry news, News, News, Ship & Shore, TechTalk