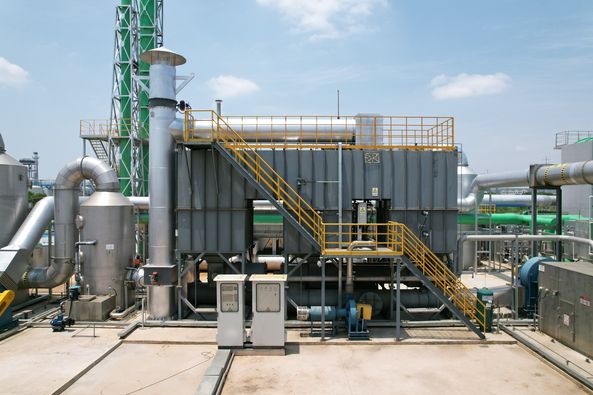
#TechTalk – RTO Ceramic Heat Exchange Media Health
October 23, 2024 8:37 am#TechTalk - RTO Ceramic Heat Exchange Media Health
RTO technology to successfully treat VOC / HAP / Odorous air emissions has always relied on the 3 Ts for efficient operation – Time (chemical residence time within the combustion chamber), proper Temperature for oxidation, and turbulence of air emissions (good mixing) to provide results.
But even a well-run and maintained RTO can naturally run into a host of issues with the health of the ceramic heat exchange media within an RTO. Depending on the process conditions – chemical attack, particulate, and condensate could cause operation concerns that might affect performance of a unit. These could include the deposition of organic and inorganic materials from the process, chemical attack (from process) which could degrade/break down the media, inadvertent transformation of chemical compounds (such as organo-silicate solvents to silica dust or glass), condensate formation, and general settling of the ceramic media itself that might result in plugging of RTO media.
Any of these will eventually restrict emission exhaust flow through the unit, affecting volumetric flow and heat exchange performance of the media. These conditions will ultimately increase pressure drop across the media resulting in higher electric consumption (fan/motor) but also impact heat exchange (fouled media, channelling of air through the media) resulting in higher natural gas consumption (burner operation). Use these as your keys if there is a slow erosion or sudden change in equipment performance.
Although a chemical attack and the general settling of ceramic media results in the need for media replacement, particulate plugging and condensate formation can be dealt with rather easily through simple washout procedures and/or oxidizer “Bake-Out” routines.
However, before conducting these types of solutions, great care is needed to properly analyze the make-up of the constituent creating the problem to verify wash or bake-out operations will work adequately, and most importantly, SAFELY.
Media Wash-Out operations are done offline in a cool RTO. High volume low pressure water flow is used to clean various ceramic media types with the RTO. Depending on the offending residue, water may or may not need to be collected for further environmental treatment. This can be done with organic and inorganic type particulates. In general, RTO performance can be brought back close to original specs, however, more stubborn silica dust type scenarios are harder to clean. Also, over numerous build-up events, cleanings slowly lose the ability to restore performance capacity, resulting in the need to replace. Equipment is then slowly dried (run on fresh air), before the equipment can be put back in service.
Bake-out procedures (think self cleaning oven), systematically elevate the temperature in the RTO to burn off organic materials that build from the process or from solvents condensing upfront of the Oxidizer. These can be done on-line or offline depending on your process. The normal operation of an RTO systematically cycles valves so heat is dispersed uniformly within an RTO. By extending a cycle in one direction through the towers, heat can be driven down lower into the ceramic chamber to burn off contaminates. By reversing the flow, the same can be done for the adjoining tower. Great care must be taken (qualified service technician on site) as this can cause great damage to equipment if done improperly.
Ship & Shore service technicians are trained to assist customers with operational techniques to extend the life of your RTO media as well as any other functioning RTO components. If you believe there may be some sort of plugging condition within your system, schedule a Ship & Shore Technician to complete your next preventive maintenance inspection.
Reach out to us at sales@shipandshore.com or call our office in Signal Hill, CA at +1(562) 997-0233 to learn more.
Categorised in: Industry news, News, News, Ship & Shore, TechTalk