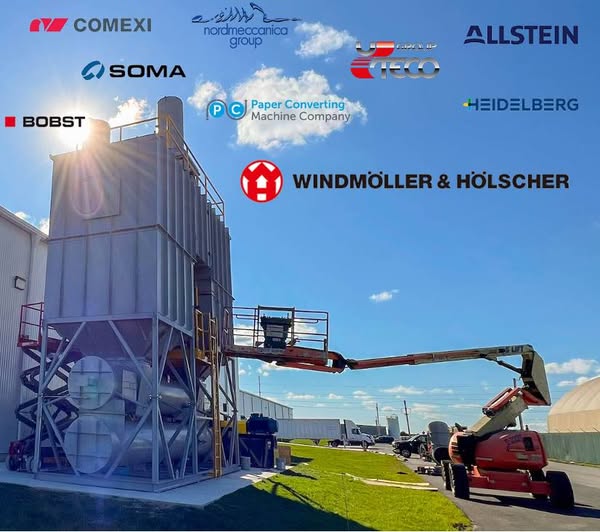
#TechTalk – Printing Industry Corona Treatment and Ozone Emissions
June 20, 2024 11:54 am#TechTalk - Printing Industry Corona Treatment and Ozone Emissions
Today’s flexographic printing press operations operate at very high speed and the efficient transfer of ink and coating materials is critical to the operation. Upstream of a coating operation, a corona treating system is designed to increase the surface energy of plastic films, foils and paper in order to allow improved wettability (Ability of ink to spread across a solid surface), promoting adhesion of inks, coatings and adhesives. As a result, the materials treated will demonstrate improved printing and coating quality, and stronger lamination strength. Proper wetting prevents smudging, smearing, or other undesirable effects.
As a by-product of the corona treatment, Ozone Emissions are generated. These emissions are very corrosive, are health adverse, and can contribute to smog also detrimental to health. Ozone emissions in the printing industry are getting more attention from the regulatory authorities, and in poor air quality areas are subject to abatement.
Depending on the amount of ozone generated, control equipment may be needed. Ozone in the atmosphere degrades rather quickly. Smaller amounts of ozone can decompose in exhaust ductwork before exiting to the atmosphere (no issue). Larger amounts need to be controlled by corona treatment systems (typically supplied by corona treatment equipment suppliers). Catalysts are used to convert the Ozone (O3 molecule) to O2 oxygen.
Ozone emissions can also be directed to the press/laminator thermal oxidizers (typically already installed/found in large scale printing operations) for ozone destruction if spare capacity is available. Typically only a few hundred cfm of exhaust capacity is needed from the treaters. Ozone is combusted in the thermal oxidizers at approximately 1500 degrees F.
Both catalyst systems and thermal oxidizer treatments meet the 8-hour, time-weighted average value of 0.1 part of ozone per million parts of air (ppm) exposure with proper process capture techniques.
In any instance, care must be taken to use exhaust ductwork fabricated from plastic or stainless steel materials to avoid corrosion in any new ductwork from the treaters or to prevent any adverse effect at the main oxidizer duct header. New ozone sources should be added into the main header as close to the oxidizer as possible, minimizing the potential of any corrosion damage.
Reach out to us at sales@shipandshore.com or call our office in Signal Hill, CA at +1(562) 997-0233 to learn more about Ozone and VOC control printing industry solutions.
Categorised in: Industry news, News, News, Ship & Shore, TechTalk