The Coil Coating process produces high end paint finishes we associate with modern appliances – washer/dryers, dishwashers, refrigerators, and much more. As best described by the National Coil Coating Association – “Coil coating is a continuous, automated process for coating metal before fabrication into end products. The steel or aluminum substrate is delivered in coil form from the rolling mills. The metal coil is positioned at the beginning of the coating line, and in one continuous process, the coil is unwound, pre-cleaned, pre-treated, pre-primed, and pre-painted before being recoiled on the other end and packaged for shipment. All of this happens at up to 700 feet per minute.”
The following steps take place on a modern coating line:
- Stitching the strip to the previous coil
- Cleaning the strip
- Power brushing
- Pre-treating with chemicals
- Drying the strip
- Applying primer on one or both sides
- Curing (often only 15 to 60 seconds!)
- Cooling the strip
- Top coating on one or both sides
- Second curing
- Cooling down to room temperature
- Rewinding of the coated coil
The use of solvent based materials in the high volume production cleaning and coating process necessitates the need for effective air pollution control to destroy volatile organic compounds (VOCs) regulated by Federal and State authorities. Abatement of VOC is typically achieved via recuperative thermal oxidizer technology or by Regenerative Thermal Oxidizers (RTOs). With either technology, pollutants are combusted at 1450 to 1500 degrees F resulting in the conversion of VOCs into primarily carbon dioxide and water, with some nitrogen oxides.
Emissions from the process are typically located in any solvent based cleaning, paint dip tank/application area, oven exhaust, and paint mix/storage rooms. Via a network of collection system ductwork, emissions are routed to an abatement device for destruction.
Recuperative Thermal Oxidizer technology employs a natural gas fired burner, combustion chamber, and integrated heat exchanger to combust emissions. The integrated air to air heat exchanger (generally up to 60% efficient) is used to preheat the incoming exhaust sources with hot (1450 to 1500F) oxidizer exhaust to minimize natural gas combustion. BTU value inherent in the VOC exhaust is more than sufficient to keep burner in low fire (pilot) position when in production. Recuperative oxidizers typically have destruction efficiencies of 99+%.
Regenerative Thermal Oxidizers (RTOs) are also used within the coil coating process. However RTOs are extremely energy efficient (95% thermal efficiency) and can achieve 98 to 99% destruction efficiency with a natural gas fired burner. The internal ceramic heat exchanger also preheats incoming process air to limit natural gas consumption. With an RTO style system, heat can be recovered from the process in a number of areas – up stream of the RTO, via the RTO combustion chamber by-pass (heat release mechanism to protect the RTO from high temperatures), and RTO exhaust.
Of keen interest in the industry is the recovery of heat from the curing ovens (operating up to 800 F) and the abatement equipment to be re-used within the process. Although there is integrated heat recovery on the abatement equipment, there is an abundance of energy that can be recovered from the process. After satisfying abatement operations heat is still recovered to heat various operations in the process.
- Steam/hot water for pretreatment cleaning.
- Hot air to preheat inlet ovens air make-up.
- Hot air to preheat emissions before abatement.
RTO technology and secondary heat recovery equipment can also qualify for rebate incentives from qualifying natural gas and electric utility providers. Ship & Shore can secure these lucrative customer incentives if available.
Over the years, Ship & Shore has worked with coil coating line builders/customers to maximize the control of emissions and energy efficiency with the supply of safe and reliable equipment.
Reach out to us at
sales@shipandshore.com or call our office in Signal Hill, CA at +1(562) 997-0233 to learn more.
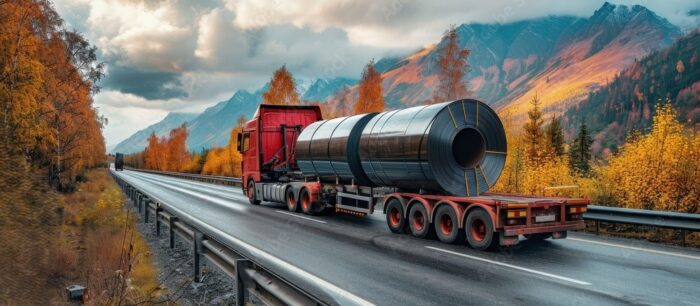