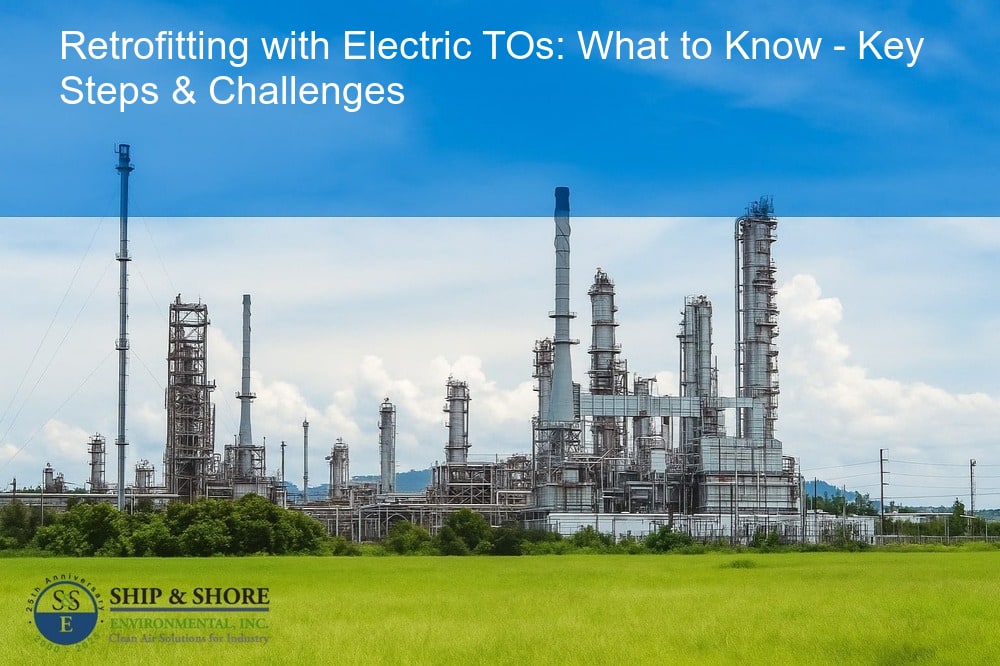
Retrofitting with Electric TOs: What to Know Before You Start
July 25, 2025 5:41 amUnderstanding the Concept of Retrofitting with Electric TOs
Retrofitting with electric TOs: what to know about modernizing your thermal oxidizer systems? This crucial question is becoming increasingly relevant as industries aim to improve operational efficiency and reduce their environmental footprint. Retrofitting involves updating existing thermal oxidizer systems to newer, more efficient electric thermal oxidizers (TOs). This transition is not merely a technological upgrade but a step towards enhancing sustainability and meeting stricter emission regulations. With advancements in electric TO technology, industries now have the opportunity to achieve significant reductions in greenhouse gases and ensure compliance with environmental standards.
The Growing Popularity of Electric Thermal Oxidizers
The demand for electric thermal oxidizers has surged in recent years, driven by their numerous advantages over traditional systems. Electric TOs are designed to efficiently manage and reduce volatile organic compounds (VOCs) and other pollutants. They are increasingly favored for their ability to achieve high destruction efficiency, typically above 99%, while minimizing operating costs. Furthermore, electric TOs do not produce direct combustion emissions, making them an environmentally friendly choice. This growing preference is a testament to their effectiveness in driving down emissions and operating costs in various industrial applications.
Importance of Retrofitting in Modern Industry
Retrofitting is no longer an optional upgrade but a vital investment for industries aiming to stay competitive and compliant. Enhanced energy efficiency, reduced operational costs, and alignment with environmental regulations are some of the key benefits of retrofitting with electric TOs. Industries across sectors, from pharmaceuticals to chemicals, are recognizing the need for more sustainable operations and are turning to retrofitting as a solution. The process not only extends the lifespan of existing equipment but also makes it possible to integrate cutting-edge technologies without the need for a complete system overhaul.
Key Considerations Before Embarking on Electric TO Retrofitting
Retrofitting with electric thermal oxidizers (TOs) is a significant investment for any industrial facility. As we journey towards sustainability, it’s imperative to consider several factors to ensure a seamless transition. First, evaluate the existing infrastructure. Some facilities may require structural modifications to accommodate the electric TOs. Additionally, consider the energy requirements and calculate the potential cost savings. Analyzing the environmental impact is equally critical. Retrofitting with electric TOs not only reduces emissions but also enhances compliance with environmental regulations.
Understanding the Technicalities: Electric TO Retrofitting Explained
Understanding the intricacies of retrofitting is crucial. The process involves replacing conventional fuel-burning thermal oxidizers with electric ones. This shift significantly reduces the carbon footprint. The electric TOs operate by using electric heaters to achieve the required temperature for oxidation. Transitioning to electric TOs entails attention to technical details. For instance, the power supply system must be robust enough to handle new electric loads. Additionally, integrating the electric TO with existing control systems ensures operational efficiency. Hence, retrofitting with electric TOs: what to know encompasses both technical and procedural aspects.
The Potential Challenges and Solutions in Retrofitting with Electric TOs
Despite the benefits, retrofitting with electric TOs does come with challenges. Here are a few potential hurdles and their solutions:
- Initial Cost: The upfront investment can be substantial. However, long-term energy savings and reduced maintenance costs offset the initial expenditure.
- Power Supply: Ensuring the facility can handle the electrical load is crucial. Upgrading the power supply infrastructure might be necessary to avoid operational disruptions.
- Downtime: Retrofitting could require temporary shutdowns. Planning and scheduling the retrofit during non-peak times minimizes production losses.
- Training: Operators and maintenance staff may need training to handle the new equipment. Invest in comprehensive training programs to ensure smooth operation.
- Regulatory Compliance: Adhering to local regulations is imperative. Consulting with environmental compliance experts ensures that all legal requirements are met.
In all these aspects, thorough planning and expert guidance play a pivotal role. By addressing these challenges proactively, we can ensure a successful retrofit with minimal disruptions.
Did you know? Retrofitting traditional thermal oxidizers with electric ones can significantly reduce greenhouse gas emissions, boosting sustainable industrial practices.
Weighing the Pros and Cons: Retrofitting with Electric TOs
As we explore the landscape of retrofitting, it is essential to weigh the pros and cons of utilizing electric thermal oxidizers (TOs). One of the primary benefits is the significant reduction in energy consumption and emissions, aligning perfectly with our environmental goals. Electric TOs offer unparalleled efficiency and can be seamlessly integrated into existing systems, enhancing overall operational performance. However, it’s vital to consider the initial investment and potential downtime during the retrofit process. Balancing these factors will help us make informed decisions for sustainable industrial practices.
Future Outlook: The Role of Electric TOs in Industrial Emission Reduction
The future of industrial emission reduction looks promising with the advent of electric TOs. As regulations around emissions tighten and industries strive to reduce their carbon footprint, the role of electric TOs will become increasingly critical. Retrofitting with electric TOs: what to know is that they not only comply with current environmental standards but also future-proof our operations against anticipated regulatory changes. By investing in electric TO technology, we are positioning ourselves as leaders in sustainable industry practices, committed to long-term environmental stewardship.
Retrofitting with Electric TOs: A Step Towards Sustainable Industry Practices
Taking the leap to retrofit our existing systems with electric TOs is more than just a compliance measure; it’s a strategic move towards sustainability. By adopting electric TO technology, we are making a statement that environmental responsibility and operational efficiency can go hand in hand. Visit our products page to explore the cutting-edge solutions we offer. Retrofitting with electric TOs: what to know is that this transition is a critical component of our journey towards a greener, more sustainable industrial future. With the right planning and execution, we can overcome any challenges and reap the benefits of modernized, eco-friendly operations.
FAQ
What are the main advantages of retrofitting with electric thermal oxidizers (TOs)?
One of the main advantages of retrofitting with electric TOs is the substantial reduction in energy consumption, which can lead to lower operating costs and a smaller carbon footprint. Additionally, electric TOs provide high efficiency and can be integrated into existing systems to enhance performance without major disruptions. Moreover, by retrofitting, we demonstrate our commitment to sustainable industrial practices and compliance with environmental regulations.
What should be considered before starting an electric TO retrofitting project?
Before embarking on retrofitting with electric TOs, it is crucial to evaluate the current infrastructure to ensure compatibility with new technology. Considerations should include the assessment of energy requirements, the availability of space for new equipment, and an analysis of the potential return on investment. Furthermore, it is important to plan for any downtime that may be necessary during the installation process to minimize impact on production.
What challenges might we face when retrofitting with electric TOs and how can we address them?
Challenges in retrofitting may include managing the initial capital investment, integrating the new technology with existing industrial processes, and training staff on new equipment. To address these, thorough planning and budgeting are essential, and seeking financial incentives for energy-efficient upgrades can be beneficial. Additionally, working with experienced professionals ensures smooth integration, while providing comprehensive training will facilitate a successful transition to the new system.
How do electric TOs contribute to sustainable industry practices?
Electric TOs make a significant contribution to sustainable industrial practices by reducing emissions and energy consumption. This aligns with our goals to not just meet, but exceed, environmental regulations and standards. Furthermore, by embracing electric TO technology, we enhance our operational efficiency, which, in turn, supports long-term sustainable growth and environmental stewardship within our industry.
What is the future outlook for retrofitting with electric TOs in terms of industry emission reduction?
The future outlook is promising, as electric TOs are expected to play a vital role in meeting stringent emission reduction targets. As industries worldwide strive for greener processes, electric TOs represent a proactive step in reducing the environmental impact of industrial activities. Consequently, retrofitting with electric TOs is a forward-thinking decision that not only meets current regulatory demands but also prepares us for a more eco-conscious future.
Categorised in: Blog