Thermal Oxidizers for Pharmaceutical Companies
Regenerative thermal oxidizers (RTO), as well as other pollution control solutions, are in increasing demand from pharmaceutical manufacturers who are facing consistent increases in demand. Pharmaceutical companies are under pressure to crack down on their emissions, which is leading to a greater need for regenerative thermal oxidizers.
The RTO’s ability to create sustainable solutions for pharmaceutical companies allows them to meet environmental targets while still manufacturing equipment, Active Pharmaceutical Ingredients (API), and medicine at the same rate.
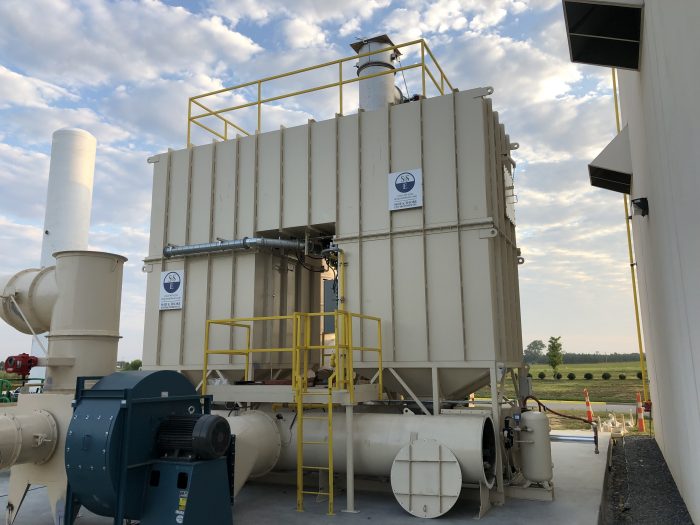

Why Do Pharmaceutical Companies Need RTOs?
Here are three key findings as to why pharmaceutical companies are in so great a need for RTOs. These particular processes need RTOs to function because they produce the highest quantity of volatile organic compound (VOC) emissions.
1. Pharmaceutical companies use the batch manufacturing method.
Many pharmaceutical companies operate in a batch system. This means that instead of producing individual versions of similar products, the products are produced on a mass scale, with modifications made to each version of the required product. Batch manufacturing is used across multiple industries and is by far the most efficient form of manufacturing.
So why does batch manufacturing require regenerative thermal oxidizers? The simple answer is that batch operations require multiple different actions to complete. For example, batch production of medicine might require heating, breaking down, re-forming, sealing, and cooling of the medicine before it is packaged. Having multiple processes occurring which include the use of alcohols, heating, and cooling equipment, produces a high level of VOC emissions. An RTO can abate the emissions from batch manufacturing while keeping its own emissions to a minimum.
2. The use of corrosive, potentially explosive, chemicals.
In the production of medicines and pharmaceutical equipment, the use of flammable chemical substances is common. This means that the lower explosive limit, or LEL, needs to be high in order to maintain adequate safety levels within the manufacturing environment. Without this, fumes and chemicals from the manufacturing process can cause explosions or fires, posing a danger to workers and a financial loss for the company.
In order to achieve a safe environment, a regenerative thermal oxidizer can abate fumes and gases within the manufacturing environment, meaning that the fumes would have to reach extortionate levels in order to catch fire and/or cause an explosion. Therefore, the RTO is a necessary safety system which secures the use of flammable substances in the manufacturing process of pharmaceutical companies, by lowering the risk of fire or explosion by a considerable amount.
3. Sterilization.
Of course, one of the key tasks in the pharmaceutical manufacturing industry is to sterilize all products. This is usually achieved by using ethylene oxide, a highly flammable substance which is designed to kill bacteria on the equipment. An RTO is 100% necessary when it comes to sterilization, in order to abate the fumes emitted during the process and create a safe working environment for employees – as well as preventing damage from fire.
Ship & Shore Advantages for Pharmaceutical Facilities
Ship & Shore Environmental has custom engineered and designed RTOs and other VOC Control Equipment for many pharmaceutical manufacturing operations over the years. We have considerable experience controlling emissions from API production, reactors, and specifically coating and drying applications. Our engineers work closely with your engineers and plant personnel to understand your process well and provide the best control technology for your operations.
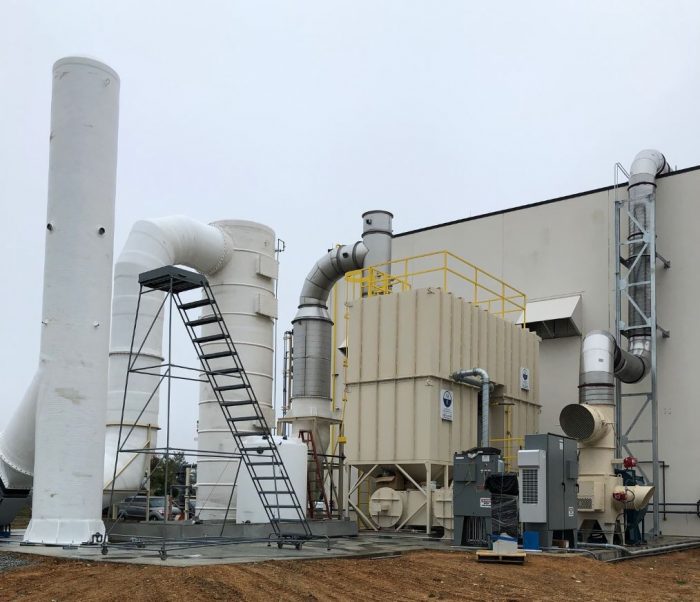