Flexographic Printing Regenerative Thermal Oxidizer
In the ever-evolving landscape of the Flexographic Printing Industry, embracing environmentally responsible practices has become a paramount consideration. The integration of Regenerative Thermal Oxidizers (RTOs) from Ship & Shore Environmental, Inc. has emerged as a pivotal solution to address air quality concerns and enhance operational efficiency. With a firm commitment to sustainability, Ship & Shore Environmental, Inc. is revolutionizing the industry by providing RTOs tailored to the unique needs of flexographic printing facilities.
Revolutionizing Air Quality with Flexographic RTOs
The Flexographic Printing Industry relies on a range of processes involving inks, solvents, and materials that can release volatile organic compounds (VOCs) into the atmosphere. These emissions not only pose environmental challenges but also impact the well-being of workers. Ship & Shore Environmental, Inc. recognizes the urgency of this issue and offers a transformative approach through RTOs. By incorporating these advanced systems, flexographic printing companies can significantly reduce VOC emissions and contribute to a cleaner environment. Ship & Shore Environmental, Inc.’s RTOs employ cutting-edge technology to capture and destroy VOCs before they are released into the air, ensuring compliance with stringent regulations and demonstrating a commitment to sustainable practices.
Efficiency Redefined with a Flexographic Printing Industry RTO
Efficiency is a hallmark of successful flexographic printing operations, and Printing Industry RTOs from Ship & Shore Environmental, Inc. amplify this efficiency to new heights. These systems not only enhance air quality but also optimize energy utilization. The innovative design of Ship & Shore Environmental, Inc.’s RTOs includes heat recovery mechanisms that harness and repurpose thermal energy generated during VOC destruction. This recovered heat is channeled back into the system, minimizing the need for additional fuel and reducing the overall environmental footprint. RTOs also offer the advantage of reliable and consistent performance, requiring minimal maintenance while ensuring uninterrupted printing processes.
The Journey Ahead: Ship & Shore RTOs for the Flexographic Industry
As the Flexographic Printing Industry embarks on a journey towards sustainability, Ship & Shore Environmental, Inc.’s RTOs serve as beacons of progress. With a focus on customizing solutions to fit specific manufacturing setups, Ship & Shore Environmental, Inc. partners closely with printing facilities to ensure seamless integration. The positive ripple effect of integrating RTOs extends beyond emissions reduction—it encompasses enhanced energy efficiency, operational reliability, and even potential incentives for energy-conscious businesses. In a world where responsible environmental practices are more crucial than ever, Ship & Shore Environmental, Inc.’s RTOs shine as catalysts of positive change in the Flexographic Printing Industry.
Frequently Asked Questions for RTOs in the Flexographic Industry
What is the primary goal of implementing RTOs in the flexographic industry?
The primary goal is to enhance air quality by reducing volatile organic compound (VOC) emissions during manufacturing processes. RTOs provide an effective solution for VOC abatement, thereby contributing to a cleaner environment and compliance with stringent regulations.
How does a Flexographic Printing Regenerative Thermal Oxidizer (RTO) contribute to energy efficiency?
The RTO’s innovative design incorporates heat recovery media, allowing it to recover approximately 95% of the heat generated during VOC destruction. This recovered heat is utilized to minimize operating fuel requirements and enhance energy efficiency.
Can Printing Industry RTOs be customized to fit specific manufacturing setups?
Absolutely. S&SE’s team of engineers and technicians collaborates closely with clients to tailor RTO systems to the specific requirements of each manufacturing facility. Customization ensures optimal performance and efficiency.
How do variable frequency drives (VFDs) enhance RTO efficiency?
VFDs are used to modulate emissions from different sources, optimizing energy conservation as the RTO operates under various conditions. This fine-tuning further enhances energy efficiency and overall performance.
What additional benefits can be gained by integrating RTOs into flexographic manufacturing processes?
Beyond VOC abatement and enhanced energy efficiency, integrating RTOs can lead to improved equipment reliability, minimized maintenance requirements, and even eligibility for cash incentives based on energy-efficiency achievements.
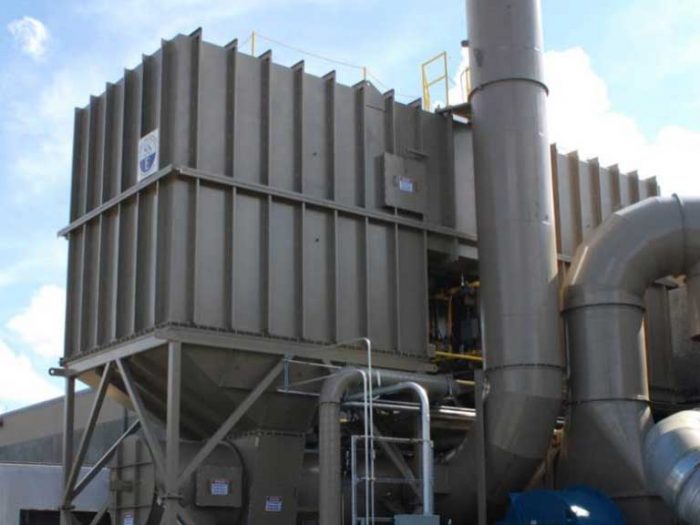