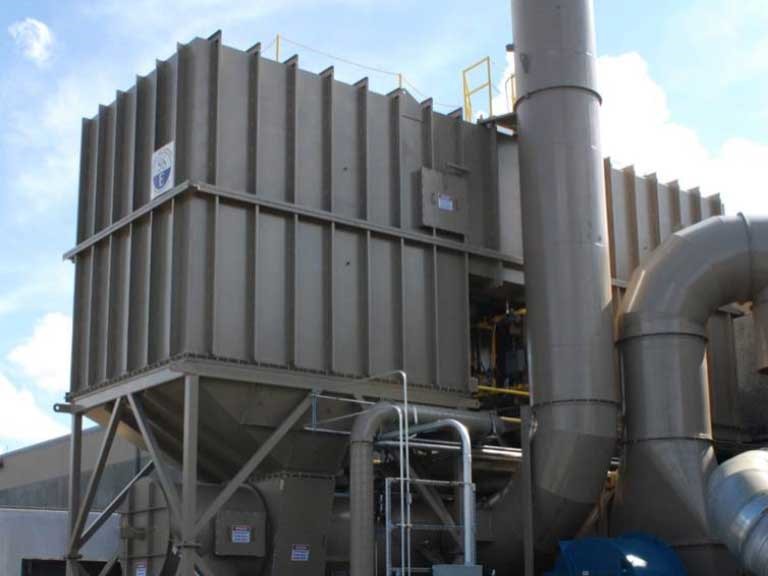
Flexographic Printing Industry – RTO Project Overview
January 4, 2017 9:25 amFlexographic Printing Industry - Ship & Shore RTO Project Overview
HISTORY
A flexographic company that produces printed wrapping and packaging materials for the floral, gift, food and confectionary industries consulted with Ship & Shore Environmental, Inc. (S&SE) to design a state-of-the-art VOC abatement system for a planned facility expansion.
The facility expansion included addition of several new pieces of manufacturing equipment. S&SE. also assisted with the air permit application process for the plant expansion.
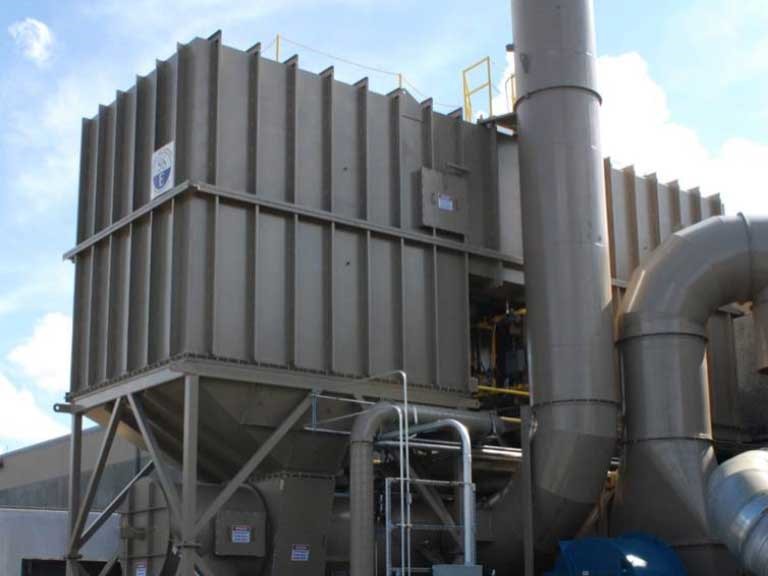
SOLUTION
In order to reduce air pollution from the facilities various manufacturing processes and to improve air quality for their workers, the customer asked Ship & Shore Environmental to develop a design that would provide a reliable and cost effective solution. S&SE team of engineers and technicians visited the facility to observe the manufacturing processes and to take flow, temperature and VOC concentration measurements. After review of the data collected by our engineering team, a recommendation was made to address all the areas of concern.
The recommended solution utilized a regenerative thermal oxidizer (RTO), VOC collection system, mixing box, and permanent total enclosure to capture and destroy the VOC emissions. The RTOs unique system design provides for an extremely energy-efficient operation. Through the use of two built-in heat exchange chambers with high-quality structured ceramic heat recovery media approximately 95% of the heat of combustion generated by the oxidation process, which destroys the collected VOCs, is recovered to minimize RTO operating fuel requirements. In addition, to further reduce oxidizer fuel consumption, the custom designed VOC collection system and permanent total enclosure (PTE) provide for optimal collection of the VOCs from each emission source in the facility. The BTUs (fuel) contributed by the VOCs collected often provide for self-sustaining operation of the RTO, allowing the burner to be shut-off after the oxidizer is brought up to operating temperature and the process emissions are brought online. A variable frequency drive (VFD) for the main process blower and mixing box is also used to modulate the emissions from the various emission sources to optimize energy conservation of the RTO as it operates under various conditions; modulating capacity as each sources is brought on and off-line. During the engineering design phase, all equipment dimensions and weights are finalized and reviewed with the customer for best configuration at the installation site.
The preliminary design for the RTO allowed for installation in a given space with minimal interruption to the existing manufacturing operations during start-up and commissioning. S&SE was instrumental in assisting the customer with the application process for cash incentives based on the energy-efficiency of the RTO. Much to the surprise of the customer the project was approved for an impressive cash incentive of more than $350,000.
Categorised in: Air pollution, Industry news, News, News, Ship & Shore, VOC Abatement