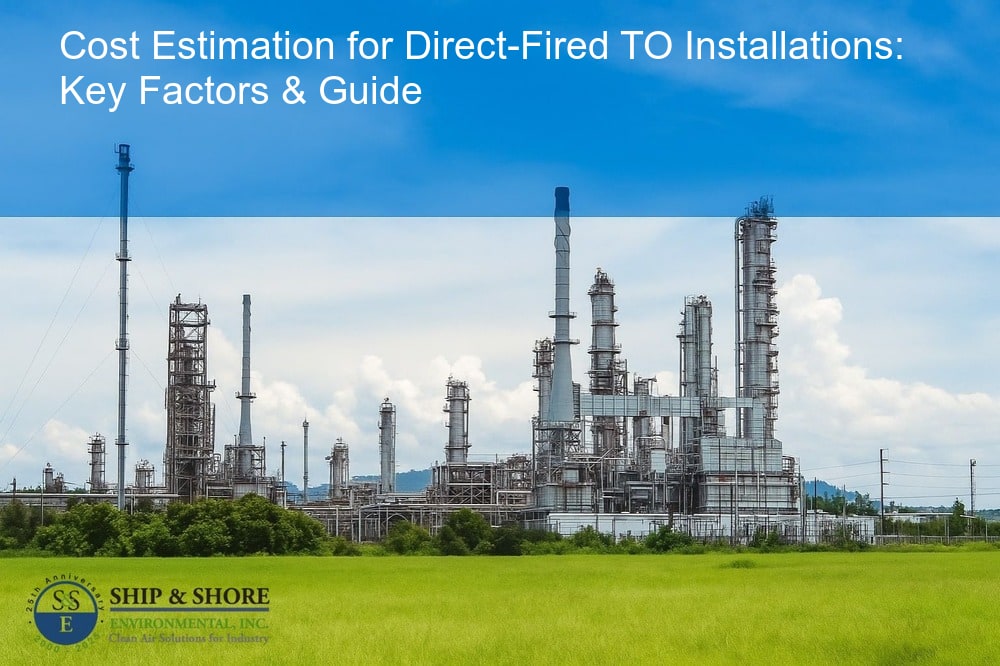
Cost Estimation for Direct-Fired TO Installations: A Detailed Guide
June 27, 2025 3:48 amUnderstanding Direct-Fired Thermal Oxidizers (TO): A Brief Overview
Direct-Fired Thermal Oxidizers (TO) are critical components in controlling industrial emissions and ensuring environmental compliance. The effectiveness and efficiency of these systems play a vital role in reducing hazardous air pollutants and volatile organic compounds (VOCs) emitted during industrial processes. As industries strive to adhere to stricter environmental regulations, understanding the cost estimation for direct-fired TO installations becomes increasingly crucial. This understanding not only aids in budgeting but also ensures that the chosen solutions are both cost-effective and compliant with regulatory standards.
The Importance of Direct-Fired TO in Industrial Emission Control
Direct-Fired Thermal Oxidizers serve as indispensable tools in the arsenal of emission control technologies. By employing high temperature combustion, these systems break down pollutants into less harmful compounds like carbon dioxide and water vapor. The capability to handle high pollutant loads, coupled with their relatively straightforward design, makes direct-fired TOs a preferred choice for many industrial applications. However, implementing these systems necessitates careful planning and cost considerations to meet both operational needs and regulatory demands effectively.
Necessity for Cost Estimation for Direct-Fired TO Installations
Investing in a Direct-Fired Thermal Oxidizer is not just about purchasing a piece of equipment; it involves comprehensive planning, installation, and long-term maintenance. Accurate cost estimation for direct-fired TO installations is therefore essential to ensure that the entire project aligns with the financial capabilities and strategic goals of the organization. By understanding the full spectrum of costs involved – from initial procurement to operational expenses – industries can make informed decisions that balance cost with performance and compliance. At Ship & Shore Environmental, Inc., we emphasize this holistic approach to cost estimation, recognizing its impact on operational efficiency and environmental responsibility.
Factors Influencing the Cost Estimation for Direct-Fired TO Installations
When considering the cost estimation for direct-fired TO installations, several critical factors must be taken into account. First and foremost, the size and capacity of the thermal oxidizer play a significant role. Larger units capable of handling higher volumes of emissions typically come with higher costs. Additionally, the complexity of the installation site, including accessibility and existing infrastructure, can substantially impact costs.
Another influential factor is the specific regulatory requirements for industrial emissions in the region where the direct-fired TO will be installed. Compliance with stringent environmental regulations may necessitate advanced technologies and materials, which can drive up costs.
The choice of materials for constructing the oxidizer itself also influences costs. High-quality materials that withstand high temperatures and corrosive environments, while more expensive up front, can reduce maintenance and replacement costs over time.
Furthermore, operational costs, including fuel consumption, maintenance, and labor, should not be overlooked. While the initial installation cost is substantial, ongoing operational costs can significantly impact the total cost of ownership.
Process Involved in Cost Estimation for Direct-Fired TO Installations
To accurately estimate costs for a direct-fired thermal oxidizer installation, a thorough process must be followed. Initially, a detailed assessment of the emission sources and the volume of pollutants to be treated is necessary. This helps determine the appropriate size and capacity of the thermal oxidizer.
Next, site surveys should be conducted to evaluate the physical space where the installation will occur. This includes assessing current infrastructure, accessibility for construction equipment, and potential modifications needed to accommodate the new system.
Quotation requests should then be sent to multiple vendors to obtain competitive pricing on the thermal oxidizer and any auxiliary equipment required. These quotations should include detailed breakdowns of costs for materials, labor, and any additional services.
Following vendor selection, a detailed cost analysis should be performed. This analysis will consider not only the direct costs of equipment and installation but also indirect costs such as permitting fees, compliance costs, and long-term operational expenses.
An often-overlooked step is factoring in contingency costs. These are additional funds set aside to cover unexpected expenses that may arise during installation, such as unforeseen site conditions or changes in regulatory requirements.
Case Study: Practical Application of Cost Estimation for Direct-Fired TO Installations
To illustrate the process, consider a case study involving a mid-sized manufacturing plant looking to install a direct-fired TO.
- First, we conducted an emissions assessment, determining the plant produced 15,000 cubic feet per minute (CFM) of volatile organic compounds (VOCs).
- Based on this, we identified the need for a thermal oxidizer with a minimum capacity of 15,000 CFM.
- Next, a site survey was performed, revealing that existing ductwork would need significant modifications to accommodate the new system.
- We obtained quotations from three reputable vendors, each offering different material and technology options.
- After selecting a vendor, we performed a detailed cost analysis, including equipment, labor, regulatory compliance, and a 10% contingency fund.
Through this methodical approach, we ensured that our cost estimation for the direct-fired TO installation was comprehensive. Moreover, this allowed us to make informed decisions, ensuring compliance, operational efficiency, and cost-effectiveness.
Did you know? Accurate cost estimation for Direct-Fired Thermal Oxidizers is essential for industries to comply with environmental regulations while ensuring cost-effective emissions control.
Addressing Common Concerns about the Cost Estimation for Direct-Fired TO Installations
When embarking on the journey of installing a direct-fired thermal oxidizer, one of the paramount concerns often revolves around the accuracy and transparency of cost estimation. It’s natural to worry about unforeseen expenses and budget overruns. At Ship & Shore Environmental, Inc., we understand these concerns deeply. Our meticulous approach to cost estimation for direct-fired TO installations involves comprehensive analysis and transparent communication to ensure you are fully aware of every cost component from the beginning. We prioritize clarity, so there are no unpleasant surprises, allowing you to plan effectively and allocate resources wisely.
The Role of Cost Estimation in Sustainable Industrial Practices
Accurate cost estimation is not just about budgeting; it’s intrinsic to the broader initiative of sustainable industrial practices. Precise financial planning enables us to assess the long-term viability and economic impact of environmental control technologies like direct-fired thermal oxidizers. By investing in thorough and accurate cost estimation, we provide our clients with the confidence to pursue clean and efficient industrial processes. Our solutions help industries meet stringent environmental regulations without financial strain, thereby promoting a balance between operational efficacy and environmental responsibility.
Final Thoughts: Making Cost-Effective Decisions in Direct-Fired TO Installations
In conclusion, making informed and cost-effective decisions in direct-fired TO installations is critical for any industrial enterprise committed to environmental stewardship and operational efficiency. We have demonstrated through various case studies that accurate cost estimation can lead to more strategic investments and long-term savings. By addressing common concerns with transparent and detailed cost analysis, we empower our clients to make decisions that are both financially sound and environmentally sustainable. Trust in our expertise to guide you through every step of the process, ensuring that your direct-fired thermal oxidizer installation is both cost-effective and environmentally responsible.
FAQ
How do we ensure the accuracy of cost estimation for direct-fired thermal oxidizer installations?
At Ship & Shore Environmental, Inc., we employ a detailed methodology that encompasses all potential expenditures. Our experienced team carefully evaluates specific project requirements, material costs, labor, design complexities, and potential contingencies to ensure our cost estimations are comprehensive and precise. Additionally, we maintain clear and ongoing communication with our clients throughout the estimation process to ensure transparency and to mitigate any concern for hidden costs.
What are the common factors that influence the price of installing a direct-fired thermal oxidizer?
The cost of installing a direct-fired TO can vary based on several factors, including the size and scale of the industrial process, the specific regulatory requirements it must meet, the complexity of the installation environment, and the types of materials being processed. Furthermore, additional features and safety systems tailored to client needs can also influence the overall investment.
Can the cost estimation process help in achieving sustainable industrial practices?
Indeed, by providing precise cost estimations, we enable our clients to effectively budget for environmental technologies, such as direct-fired TO systems. Consequently, this supports the implementation of cleaner, more efficient processes that align with sustainability goals. Precise budgeting is vital for reducing the risk of cost overruns, thereby ensuring both financial and environmental objectives are met.
How does Ship & Shore Environmental, Inc. address concerns about potential additional costs post-installation?
We understand the importance of maintaining a transparent relationship with our clients. Aside from the initial cost estimation, our team diligently accounts for potential operating expenses, maintenance costs, and efficiency evaluations to provide you with a holistic view of your total investment over time. This proactive approach allows us to maintain cost-effectiveness and reliability throughout the lifespan of your direct-fired TO system.
What steps do we take to ensure our clients make cost-effective decisions when installing direct-fired TO systems?
Our approach revolves around not only meeting immediate budgetary needs but also considering long-term operational costs. We conduct a thorough analysis of your industrial processes and emission control needs, followed by a cost-benefit evaluation of possible solutions. This enables us to recommend the most efficient and cost-effective direct-fired TO systems. Moreover, our commitment to leveraging cutting-edge designs and technologies ensures optimized performance and cost savings over the life of the system.
Categorised in: Blog