Coil Coating
What is Coil Coating?
Coil coating is a mechanical process that is used to apply a protective layer onto metal coils, typically made of steel or aluminum, in a continuous and automated manner. This process involves cleaning and preparing the metal surface before applying a layer of paint or other coating material using a roller or flow coating. The coated metal coil is then baked in an oven to cure the coating, resulting in a consistent and long-lasting finish.
Coil coating is a process commonly utilized in the production of various items such as building panels, metal roofs, automotive parts, and household appliances. It provides various advantages, including better corrosion resistance, increased durability, and improved aesthetics. Moreover, coil coating is a more efficient and economical method compared to traditional painting methods as it enables a quicker production rate and decreases the requirement for manual labor.
Working Process
In the coil coating process, the metal coil undergoes several steps. First, it is unwound, cleaned, and pre-treated. Then, a finish coat is applied onto a flat continuous sheet and subjected to heat curing. After curing, it is cooled and rewound for shipment. At the fabricator’s facility, the coated coil is cut to the desired size and shaped into its final form.
Compared to other application methods, coil coating is highly efficient. The application is carried out at very high line speeds. The applied paint is cured within a short time frame of 15 to 45 seconds. Unlike spray-applied coatings, coil-coated surfaces offer a uniform film thickness, avoiding the thicker films typically found on edges, corners, and bends.
How it Generates Pollution
While coil coating itself does not generate pollution, certain aspects of the process can contribute to pollution if not managed properly. Here are some potential sources of pollution associated with coil coating:
- Volatile Organic Compounds (VOCs): Coil coating involves the use of solvents, primers, and coatings that may contain volatile organic compounds (VOCs), which can evaporate into the air during the application and curing processes, contributing to air pollution.
- Hazardous Waste: Coil coating often generates waste materials such as spent solvents, paint residues, and cleaning agents.
- Air Emissions: In addition to VOCs, the coil coating process may also release other air pollutants such as particulate matter and hazardous air pollutants (HAPs) from combustion processes, drying ovens, or coating application equipment.
- Energy Consumption: Coil coating involves the use of energy for different operations like heating, curing, and drying. The type of energy sources employed, such as fossil fuels or electricity produced from fossil fuels, determines the level of energy consumption associated with the process. This energy consumption can contribute to the emission of greenhouse gases and air pollution.
- Water Pollution: Coil coating generally includes cleaning and rinsing procedures that can result in the generation of wastewater containing pollutants such as metals, paint residues, and cleaning chemicals.
Controlling Pollution from Coil Coating Processes
To control pollution from coil coating processes, it is necessary to take a comprehensive approach that addresses various aspects such as emissions reduction, waste minimization, and adoption of environmentally friendly practices. Here are some strategies that can assist in controlling pollution in coil coating industries:
- Use Clean Technologies: Invest in modern and efficient equipment that reduces emissions and optimizes resource consumption. Consider implementing advanced air pollution control systems, such as Regenerative Thermal Oxidizers (RTOs) to capture particulate and treat VOC/HAP emissions.
- Implement Waste Management Systems: Develop a robust waste management plan to minimize the generation of hazardous waste. This can include recycling and reusing materials whenever possible and properly disposing of any waste that cannot be recycled.
- Optimize Coating Processes: Review and optimize coating processes to minimize the release of VOCs, which are a significant contributor to air pollution. Use low-VOC or water-based coatings, and ensure proper ventilation systems are in place to control and capture any emissions.
- Practice Energy Conservation: Reduce energy consumption by implementing energy-efficient practices throughout the production process.
- Employee Training and Awareness: Provide comprehensive training to employees about pollution control measures and the importance of environmental responsibility.
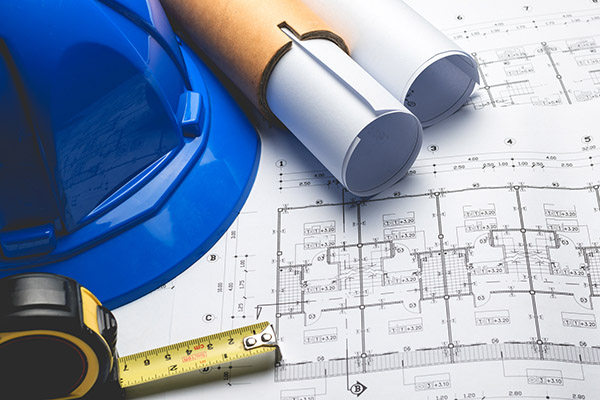