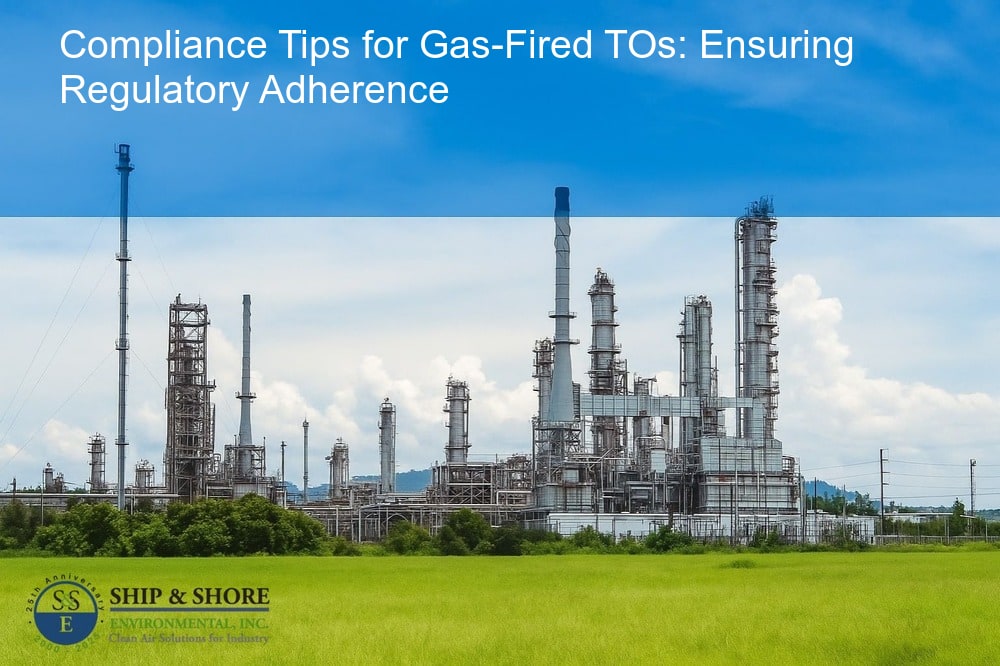
Essential Compliance Tips for Gas-Fired TOs Operations
June 30, 2025 8:17 amUnderstanding the Basics of Gas-Fired TOs
Gas-fired thermal oxidizers (TOs) are critical components in various industrial processes that work to control air pollution by oxidizing hazardous emissions. Ensuring that these systems operate efficiently and in line with regulatory requirements is crucial. One of the most important aspects to focus on is adherence to compliance regulations. Our guide on compliance tips for gas-fired TOs provides valuable insights into maintaining regulatory standards. Adhering to these guidelines not only supports environmental sustainability but also safeguards your operations from potential legal and financial repercussions.
The Importance of Compliance in Operating Gas-Fired TOs
Operating a gas-fired TO involves more than just general maintenance and operation. It requires a nuanced understanding of environmental regulations that govern emissions and operational standards. Compliance is pivotal because it ensures that the TOs are functioning optimally, minimizing harmful emissions, and meeting legal standards. Failure to comply can result in significant fines, legal action, and damage to your company’s reputation. Beyond the legal aspect, operating within compliance improves the overall efficiency of the thermal oxidizer, leading to better performance and long-term operational savings.
Key Components of Regulatory Standards for Gas-Fired TOs
Regulatory standards for gas-fired TOs typically encompass a range of criteria, from emission limits to operational practices and record-keeping. Parameters such as maximum allowable emission levels, proper operation and maintenance protocols, and thorough documentation of processes are all critical components of these standards. Understanding these elements is essential for ensuring that your TOs are not only effective in controlling pollution but also aligned with environmental laws and best practices. Regular audits and inspections are often part of these regulatory frameworks, emphasizing the need for continuous vigilance and adherence to established guidelines.
Compliance Tips for Gas-Fired TOs: The Fundamentals
To run gas-fired thermal oxidizers (TOs) efficiently, understanding and implementing compliance measures is paramount. We need to do more than meet regulatory expectations; we must exceed them. A strong foundation in compliance results in better performance, safety, and sustainability, ultimately enhancing overall operations. For this reason, Ship & Shore Environmental, Inc. offers key insights and practical advice on maintaining compliance in the use of gas-fired TOs.
Risks & Consequences of Non-compliance in Operations of Gas-Fired TOs
Operating outside of regulatory boundaries isn’t just illegal; it can also be costly and dangerous. Fines and penalties are a given, but the risks extend beyond financial losses. Non-compliance can lead to operational shutdowns, damaged equipment, and even legal action. Furthermore, non-compliance poses significant health and safety hazards, which compromise our workforce’s well-being. Ensuring compliance mitigates these risks, fostering a safer and more reliable work environment.
Practical Steps Towards Achieving and Maintaining Compliance for Gas-Fired TOs
- Regular Inspections: Conduct routine inspections to ensure all components are functioning optimally. Identifying potential issues early prevents costly repairs down the line.
- Record Keeping: Maintain detailed records of all inspections, maintenance activities, and any changes in operations. These logs are crucial for compliance audits.
- Training: Continuous staff training is fundamental. Well-informed employees are better equipped to maintain compliance and identify potential hazards.
- Update Equipment: Invest in the latest technology and equipment designed to meet or exceed compliance standards. Up-to-date systems enhance both efficiency and safety.
- Engage Experts: Sometimes, external audits by professionals can provide valuable insights and identify areas requiring improvement. Partnering with compliance experts ensures that all regulatory criteria are met.
Each of these steps is essential in fostering an environment where compliance is a routine part of our operations. By committing to these practices, Ship & Shore Environmental, Inc. ensures that our gas-fired TOs not only meet but surpass industry standards.
Did you know? Non-compliance in gas-fired TO operations can lead to legal penalties, increased accidents, and higher emissions, undermining sustainability efforts.
The Role of Compliance in Sustainable and Efficient Operations of Gas-Fired TOs
Ensuring compliance in the operation of gas-fired thermal oxidizers (TOs) is paramount for achieving sustainability and efficiency. Not only does compliance with regulatory standards uphold the integrity of our operations, but it also safeguards the environment and public health. By adhering to established guidelines, we minimize harmful emissions and reduce the risk of legal and financial repercussions that can arise from non-compliance. Furthermore, understanding and integrating compliance into the core of our operations can streamline processes, leading to improved operational efficiency and cost savings. It is crucial to recognize that compliance is not just a legal obligation but a commitment to responsible and ethical business practices.
Future Trends: Compliance Reporting for Gas-Fired TOs
As we look toward the future, compliance reporting for gas-fired TOs is expected to evolve. Advances in technology are paving the way for more sophisticated monitoring and reporting tools. Automated systems and real-time data analytics are becoming essential components in ensuring continuous compliance. These innovations enable us to detect and address potential compliance issues promptly, thereby enhancing our ability to maintain high environmental standards. Additionally, regulatory agencies are increasingly adopting stringent measures to ensure transparency and accountability. Staying ahead of these trends by investing in advanced compliance solutions will position us favorably in a rapidly changing regulatory landscape.
Recap: Key Takeaways from the Compliance Tips for Gas-Fired TOs
To recap, our focus on compliance tips for gas-fired TOs has highlighted several critical points. First, understanding the regulatory framework and the specific requirements applicable to our operations is fundamental. It is essential to familiarize ourselves with the key components of regulatory standards and continuously monitor any updates or changes. Second, the risks and consequences of non-compliance cannot be overstated. Non-compliance can lead to severe penalties, operational shutdowns, and reputational damage. Lastly, practical steps such as regular audits, employee training, and maintaining accurate records are vital in achieving and maintaining compliance. By implementing these measures, we can ensure that our operations align with regulatory standards and contribute positively to environmental conservation.
At Ship & Shore Environmental, Inc., we are committed to upholding the highest standards of compliance. Our abatement design solutions are meticulously crafted to meet regulatory requirements while optimizing performance. As we continue to navigate the complexities of compliance, our dedication to sustainable practices and innovative solutions remains unwavering. By staying informed and proactive, we can foster an environment of continuous improvement and operational excellence.
FAQ
What are the key components of regulatory standards for gas-fired TOs?
The key components often include emissions limits, operational parameters, regular monitoring and reporting requirements, safety protocols, and periodic maintenance checks. Understanding these components is vital to ensuring full compliance and maintaining operational efficiency with our gas-fired TOs.
What risks are associated with non-compliance in the operation of gas-fired TOs?
Non-compliance can lead to significant legal penalties, operational disruptions, negative environmental impacts, and tarnished company reputation. Additionally, there is the potential for increased operational costs due to fines and the need for emergency corrective actions.
How can we achieve and maintain compliance for our gas-fired TOs?
Maintaining compliance involves regular audits, comprehensive staff training, investing in up-to-date monitoring equipment, keeping precise records, and staying informed about regulatory changes. Importantly, a proactive approach and commitment to continuous improvement are essential for sustainable operations.
How does ensuring compliance with regulations contribute to operational sustainability?
Compliant operations minimize environmental impact through reduced emissions, fostering a relationship of trust with stakeholders and regulators. Consequently, sustainable practices lead to long-term operational viability and can contribute to cost savings through efficient resource utilization.
What are the future trends in compliance reporting for gas-fired TOs?
The future of compliance reporting is gearing towards more advanced monitoring systems and real-time data analytics for improved accuracy and transparency. Embracing these technologies supports proactive compliance management, ensuring we stay at the forefront of sustainable practices.
Categorised in: Blog