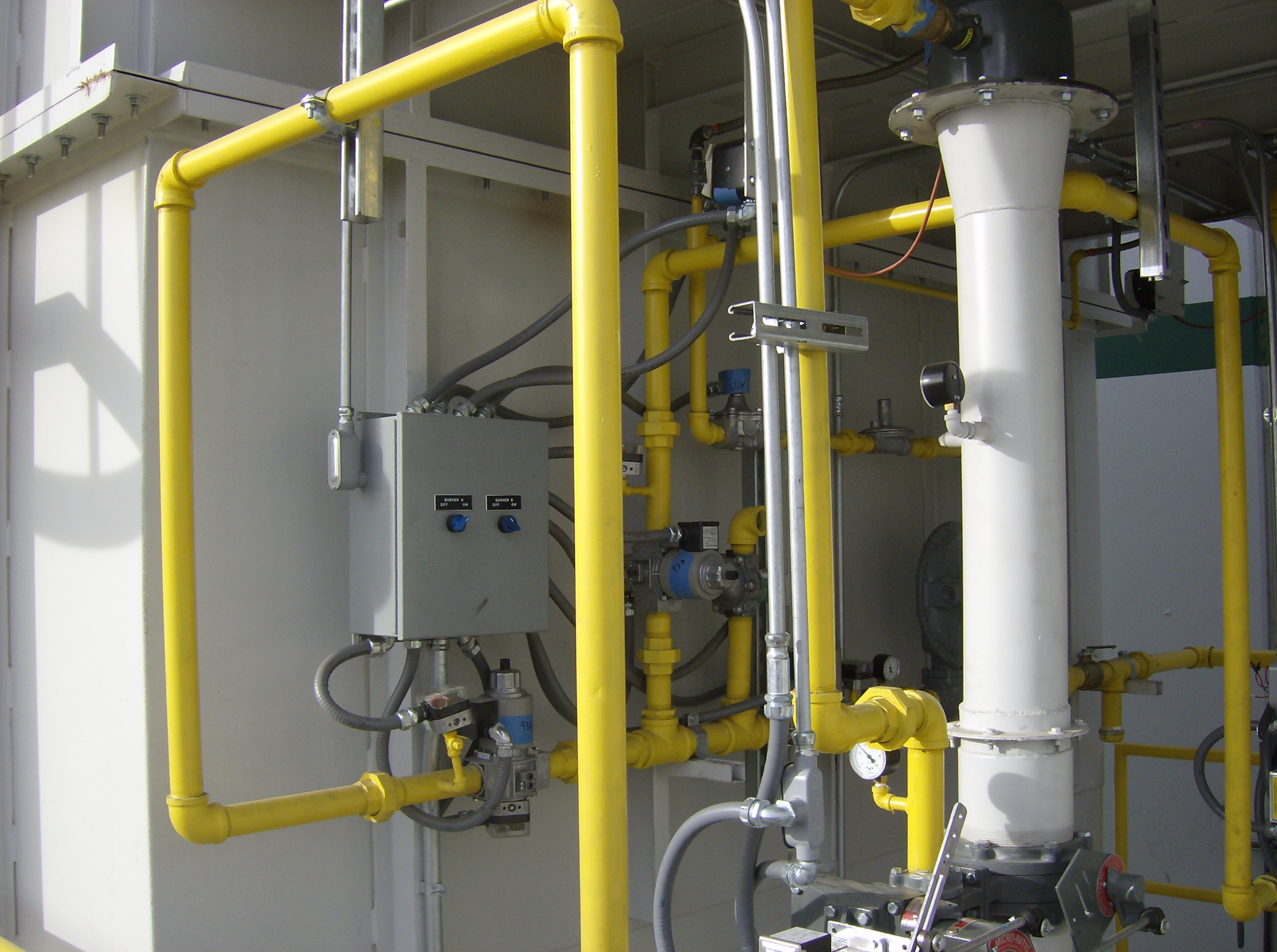
Commercial Oxidizer, Oven & Furnace Safety & Standards per NFPA 86
July 21, 2016 4:44 pmCommercial Oxidizer, Oven & Furnace Safety & Standards per NFPA 86
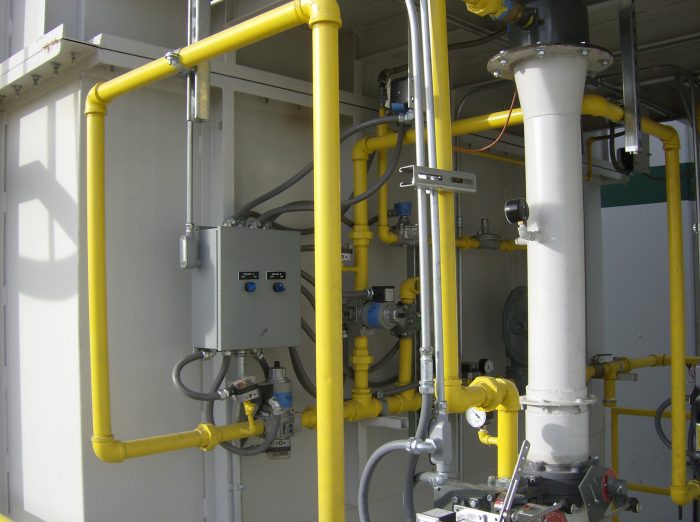
Commercial oxidizers, ovens and furnaces fall under strict regulations. Ship & Shore helps companies comply with not only air pollution equipment compliance but the NFPA that also deals mostly with the safety issues involved with industrial technology like the regenerative thermal oxidizers we manufacture at Ship & Shore. Below id the most updated information from Chapter 3 of NFPA 86.
For assistance in further understanding the regulations and more when in comes to the operation and compliance issues associated with thermal oxidizers and the technology please contact our engineering department at +1(562)997-0233 or email us by clicking here.
- Afterburner (Direct Thermal Oxidizer) is a direct thermal oxidizer, installed in series and downstream of process equipment, that generates VOC or HC; also referred to as secondary combustion chamber.
- Direct Thermal Oxidizer is a combustion system in which the burner(s) directly heats VOCs or HCs to the destruction temperature without heat recovery to the incoming gases.
- Direct Catalytic Oxidizer is a combustion system in which the burner(s) directly heats volatile organic compounds (VOCs) or hydrocarbons (HCs) to the destruction temperature, prior to their introduction to a destruction catalyst, without heat recovery to the incoming gases, and in which the catalytic destruction temperature is lower than the non-catalytic (direct thermal) destruction temperature.
- Fume incinerators
- Recuperative Thermal Oxidizer is a combustion device in which the burner(s) directly heats VOCs or HCs to the destruction temperature and in which the hot products of combustion are used to indirectly heat the incoming gas stream before it contacts the burner flame.
- Recuperative Catalytic Oxidizer is a combustion system in which the burner(s) directly heats VOCs or HCs to the catalytic destruction temperature prior to their introduction to a destruction catalyst, after which products of combustion are used to indirectly heat the incoming gas stream before it contacts the burner flame, and in which the catalytic destruction temperature is lower than the non-catalytic (direct thermal) destruction temperature.
- Regenerative Thermal Oxidizer is a combustion device in which the burner(s) directly heats VOCs or HCs after the gas stream is preheated to the destruction temperature by the periodic flow reversal of the gas stream through heat storage media that alternately have been heated by the product gases during an exhaust cycle and then have given up their heat to the incoming reactant gases during an inlet cycle.
- Regenerative Catalytic Oxidizer (RCO) is a combustion system in which the burner(s) directly heats VOCs or HCs after the gas stream is preheated to the destruction temperature by the periodic flow reversal of the gas stream through beds of ceramic heat recovery media with a coating or layer of catalyst that alternately have been heated by the product gases during an exhaust cycle and then have given up their heat to the incoming reactant gases during an inlet cycle.
- Flameless Thermal Oxidizer is a direct recuperative or regenerative combustion system in which the burner(s) preheats the heat storage media prior to the introduction of VOCs or HCs and in which, subsequently; the destruction is carried out in interstices of the heat storage media in a flameless self-sustaining manner.
NFPA 86 requires a management system be in place to maintain and prevent hazards with all oxidizer system and some of the regulations are the following:
Burner Management System (BMS) includes field devices, logic system, and final control elements dedicated to combustion safety and operator assistance in the starting and stopping of fuel preparation and burning equipment and for preventing mis-operation of and damage to fuel preparation and burning equipment.
Burner management system logic shall be tested and verified for compliance with the design criteria when the burner management system logic is installed, replaced, repaired, or updated.
Burner Management System Logic includes the following list of requirements that are common to various burner and BMS codes.
- Mandatory Purging
Correct pre-ignition purging of the combustion chamber is crucial to the safe operation of the system to prevent the possibility of an accumulation of combustible gas followed by
accidental or improper ignition sequence resulting in an explosion. - Permissive Interlocks
Typical interlocks would include high/low fuel and pilot gas pressure, high/low stack
temperature, loss of flame, high/low firebox pressure, loss of combustion air, and any
additional trips that may be required due to the design or configuration of the burner
chamber. - Double Block and Bleed Systems
The safety shut-off valves are the key component in the BMS to prevent the accumulation of an explosive mixture in the burner chamber. Standard practice is to provide automated
safety shutoff valves installed in a double block and bleed configuration on the main and pilot headers, except for radiant tube–fired burner systems. An additional safety shut-off valveshould be located on each individual burner for multiple burner systems. - Pilots and Ignition Systems
Typically each burner is provided with its own pilot and ignition system. The igniter lights the pilot burner which then in turn lights the main burner. - Dedicated Flame Monitoring Systems
Each burner is equipped with its own flame monitoring device with independent detectors are required to supervise the pilot and the main flame. Exceptions may be made depending on the type of pilot and burner. Typically a self checking UV (Ultraviolet) or IR (Infrared) Scanner is used to monitor the main flame. - High / Low Pressure, Temperatures and Flow
Dependant on the process, high/low process flow/pressure alarms as well as temperature
may be required to prevent operation outside the design parameters. - Combustion Air and Draft Pressure Alarms and Controls
Combustion Safeguard is a safety device or system that responds to the presence or absence of flame properties using one or more flame detectors and provides safe start-up, safe operation, and safe shutdown of a burner under normal and abnormal conditions.
Flame Detector is a safety device directly responsive to flame properties that senses the presence or absence of flame using flame sensors.
Flame Failure Response Time is the period of time that starts with the loss of flame and ends with the de-energizing of the safety shutoff valve(s).
Hardwired is a dedicated interconnection for each individual signal or interlocks to a logic system or between logic systems.
Pressure Regulators shall be furnished wherever the plant supply pressure exceeds the burner operating or design parameters or wherever the plant supply pressure is subject to fluctuations. Otherwise an automatic flow control valve shall be permitted to meet the requirement above, provided it can compensate for the full range of
expected source pressure variations.
Regulators, relief valves, and switches shall be vented to an approved location that meets the following criteria:
(1) Heavier-than-air flammable gases shall be vented outside the building to a location where the gas is diluted below its LFL before coming in contact with sources of ignition or re-entering the building.
(2) Vents shall be designed to prevent the entry of water and insects without restricting the flow capacity of the vent. PLCs.
Where used for combustion safety service, safety PLCs shall have the following characteristics:
(1) The processor and the I/O shall be listed for control reliable service with an SIL rating of at least 2.
(2) Access to safety functions shall be separate from access to non safety functions.
(3) Access to PLC logic dedicated to safety functions shall be restricted to prevent unauthorized changes.
(4)All safety function sensors and final elements shall be independent of operating sensors and final elements.
PLCs shall not implement the following:
(1) Manual emergency switches
(2) Continuous vapor concentration high-limit controllers
Ship & Shore helps manufacturers maintain compliance with complete environmental solutions for air pollution abatement and energy and heat recovery systems for maximum efficiency and cost effective operations. Call or Email us today to see how current and coming regulations may affect your manufacturing application. Your project may be eligible for significant cash incentives from energy efficiency programs! Call +1(562)997-0233 or EMAIL us by clicking here.
Categorised in: Air pollution, News, News, Technical