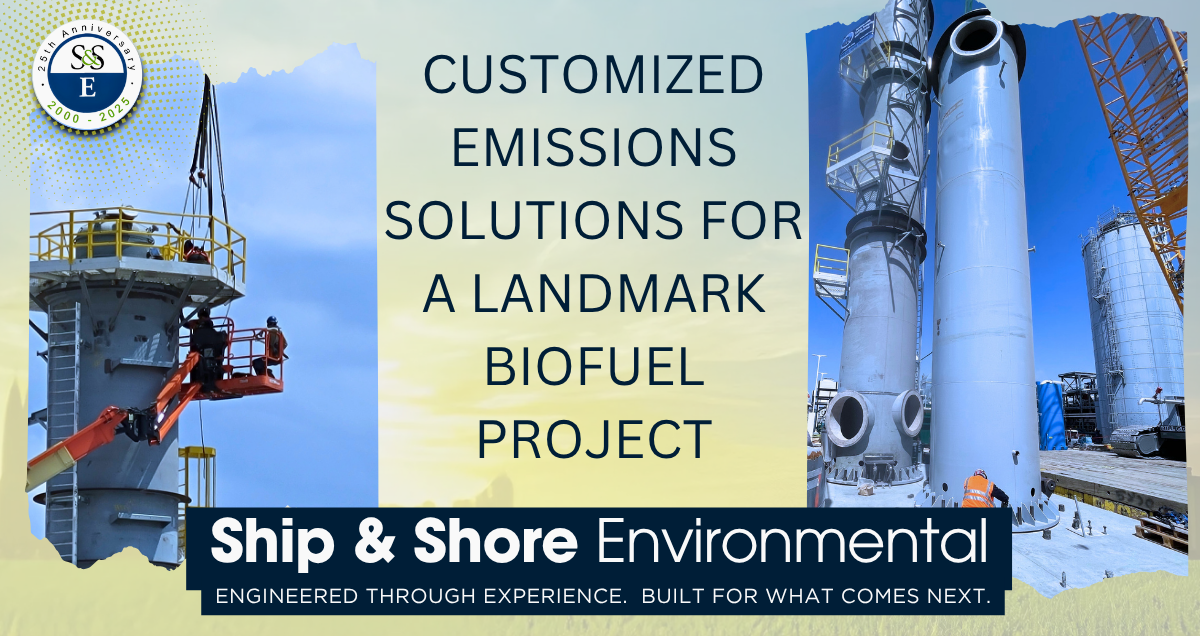
CASE STUDY: Southern California Bioenergy Facility – Customized Emissions Solutions for a Landmark Biofuel Project
July 9, 2025 8:00 amCase Study: 7.9.2025
DFTO system installed at So Cal Bioenergy Facility – Customized Emissions Solutions for a Landmark Biofuel Project “
How Ship & Shore Environmental (S&SE) Delivered a Customized High-Performance Direct-Fired Thermal Oxidizer Air Pollution Control system for One of America’s Largest Organics-to-Energy Plants
- · Emitting Process: Flue gas From Pyrolyzer
- · VOC Profile: High Sulfur & Nitrogen waste mercaptan, SOx and NOx <200 ppm
- · Exhaust Volume: 35,000 ACFM @ 750°F
- · CleanAir Solution: Direct-Fired Thermal Oxidizer (DFTO) with integrated NOx abatement
- · Destruction Efficiency: ≥99% VOC DRE
- · Project Solution: 70-foot, 102-ton DFTO unit; heat exchanger; vertical stack, and booster fan
Overview
In the heart of Southern California’s bustling Inland Empire, the Bioenergy Facility stands as a beacon of innovation in organics-to-energy technology. As one of the nation’s leading biofuel operations, the Bioenergy facility transforms organic waste into renewable energy, playing a critical role in California’s environmental and energy landscape. Yet, with this vital mission comes the challenge of stringent air quality compliance—particularly under the watchful eye of the South Coast Air Quality Management District (AQMD), arguably one of the leading authorities in environmental compliance enforcement. The following is how S&SE’s customized Direct-Fired Thermal Oxidizer came to be:
To sustain high-capacity operations and strict uptime demands, the Bioenergy Facility required a robust, high-efficiency air pollution control solution. The facility needed to meet tight emissions limits for volatile organic compounds (VOCs) and nitrogen oxides (NOx), all while operating a process system with substantial airflow and temperature requirements. S&SE, renowned for its expertise in industrial emissions abatement, was called upon to design, deliver, and support a tailored solution.
The Challenge
The Bioenergy Facility’s needs were complex. The centerpiece of the emissions control system was a 70-foot tall vertical 2 stage Nox Reducing Direct-Fired Thermal Oxidizer (DFTO), weighing in at over 102 tons. Beyond the sheer scale, the DFTO required precision engineering to integrate with the facility’s process streams and ensure optimal thermal performance.
Key technical and logistical challenges included:
- Massive Scale & Weight: Delivering and erecting a 70-foot, 102-ton oxidizer demanded advanced rigging, transportation, and installation methodologies. The size and weight necessitated careful site planning, route analysis, and coordination with local authorities.
- Thermal Integration: The system needed to seamlessly capture and recycle heat energy to maximize process efficiency, including a sophisticated heat exchanger to recover flue gas and provide oil heating elsewhere in the plant.
- NOx Abatement: The required a solution that not only destroyed VOCs but also incorporated advanced NOx controls to meet or exceed South Coast AQMD’s regulatory standards.
- Site Constraints: The facility’s urban location and compact footprint left little room for error in system layout and installation, increasing the importance of modular, adaptable design.
- Uninterrupted Operations: Downtime was not an option. S&SE’s installation and commissioning strategies needed to ensure minimal disruption to ongoing facility activities.
Why Ship & Shore Environmental?
The Bioenergy facility project team selected S&SE for several strategic reasons:
- Proven Experience: S&SE’s extensive track record in designing and fabricating large-scale DFTO systems gave the client confidence in both technical capability and project execution.
- Advanced Engineering Expertise: S&SE’s team demonstrated deep knowledge in integrating their VOC and NOx emissions control abatement technologies, ensuring the proposed system would not only meet but exceed emissions control targets.
- Proximity & Responsiveness: Located within Southern California, S&SE was uniquely positioned to provide responsive service, on-site supervision, and rapid turnaround throughout all project phases.
- Commitment to Local Manufacturing: A “Made-in-America” approach ensured quality control, reliable timelines, and supply chain resilience—all aligned with BIOENERGY FACILITY’s environmental and operational values.
S&SE’s DFTO Solution:
Working in close collaboration with the client’s engineering and operations teams, S&SE developed a multi-stage DFTO system, precisely calibrated to the facility’s specifications:
- Direct-Fired Thermal Oxidizer (DFTO): Capable of processing up to 35,000 ACFM at 750°F, the custom-built oxidizer efficiently destroys hazardous pollutants while maximizing thermal transfer.
- NOx Abatement Technology: The DFTO was seamlessly integrated with advanced NOx reduction components, aligning with AQMD’s strictest emissions standards.
- Energy Recovery Heat Exchanger: The design included a robust heat exchanger to recycle flue gas energy, transferring it to oil heating systems elsewhere in the plant—an innovation that simultaneously boosted efficiency and sustainability.
- Full Lifecycle Service: S&SE provided end-to-end supervision, from design and engineering through manufacturing, delivery, installation, and commissioning. Local support enabled rapid troubleshooting and minimized commissioning time.
- hands-on partner, addressing challenges as they arose and supporting post-installation performance.
Client Feedback
“Customer was very pleased with S&SE’s continuous support throughout the genesis of the project to the field installation.”
— Jean Goueth, Senior Process Engineer
Conclusion
The Bioenergy Facility project highlights S&SE’s ability to deliver high-performance, custom-engineered solutions for even the most challenging emissions control projects in the biofuel sector. With deep technical expertise, local manufacturing capabilities, and a commitment to continuous client support, S&SE is the partner of choice for organics-to-energy facilities seeking a competitive edge in compliance, efficiency, and operational reliability.
S&SE’s successful collaboration with the Bioenergy Facility showcases how innovation, experience, and a client-focused approach can turn complex environmental challenges into opportunities for sustainable growth. From concept to compliance, S&SE’s solutions are paving the way for a cleaner, more resilient future in the bioenergy industry.
Tags: BIOFUEL, Case Study, DFTO, NOx, Ship and Shore Environmental, SSE, SSE25Years, SSECleanAir, SSEDFTO, VOC abatementCategorised in: Biogas, Case Study & White Papers, Industry news, News, Ship & Shore, Technical, VOC Abatement