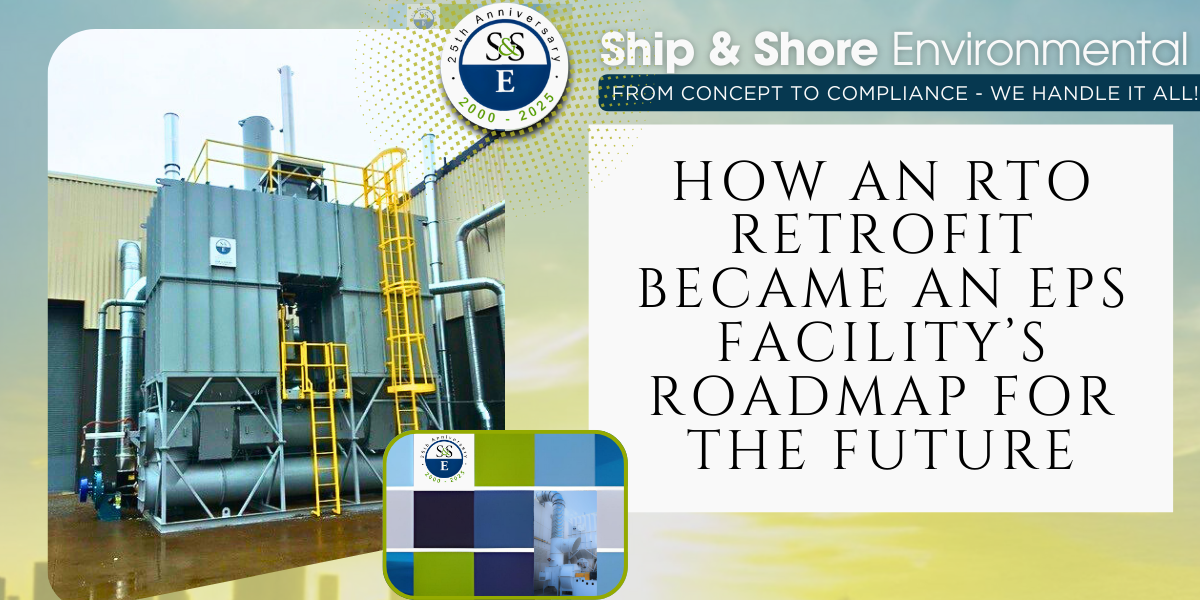
CASE STUDY: How an RTO Retrofit Became a Roadmap for the Future of One EPS Facility: A 17,000 SCFM Story
May 14, 2025 8:18 am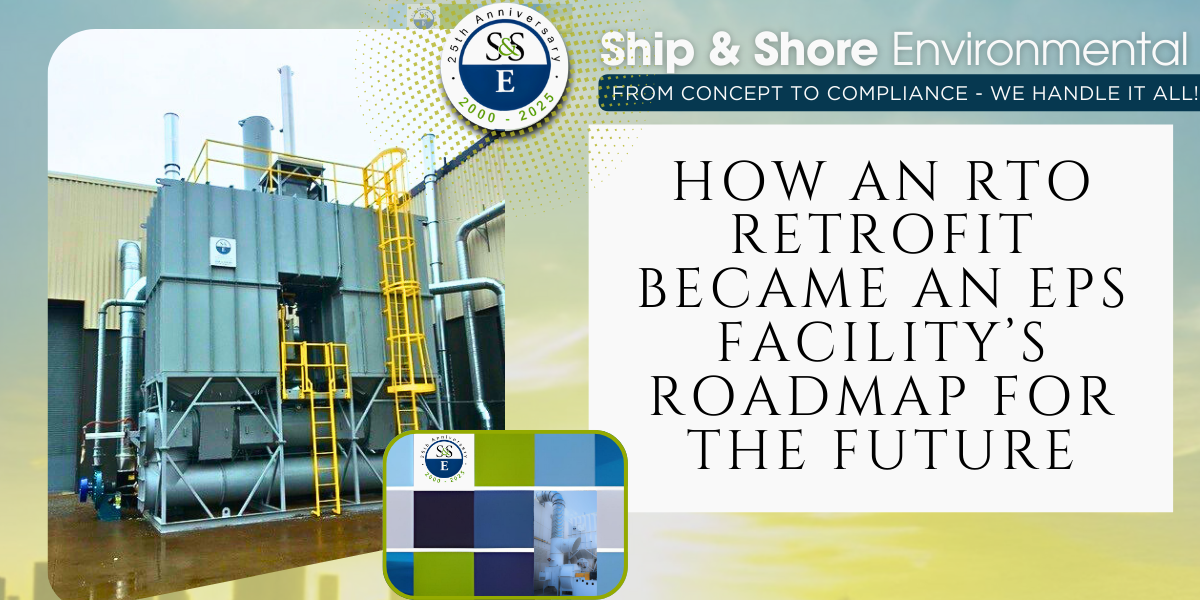
CASE STUDY: How an RTO Retrofit Became a Roadmap for the Future of One EPS Facility: A 17,000 SCFM Story
Industry: Expanded Polystyrene (EPS)
System: 17,000 SCFM Regenerative Thermal Oxidizer
Mission: Tame pentane emissions. Achieve compliance. Maximize uptime.
The Situation
Expanded Polystyrene (EPS) is everywhere — packaging, insulation, and beyond. But behind its lightweight convenience? A heavy VOC burden, thanks to pentane. For EPS manufacturers, staying ahead of air quality regulations isn’t just important — it’s existential.
That’s where Ship & Shore Environmental stepped in.
The Challenge
This facility was at a crossroads. Mounting environmental regulations. Risk of non-compliance. And a need for serious technology to meet strict VOC destruction requirements — without disrupting production.
The question wasn’t if they needed an air pollution control solution.
It was how fast they could get one that actually worked.
The Solution: A Custom-Built 17,000 SCFM RTO
We didn’t just deliver an oxidizer. We delivered peace of mind.
Here’s what we engineered — from the ground up — for this EPS operation:
- 98% VOC Destruction Efficiency
- 95% Thermal Energy Recovery
- Custom Add-Ons That Matter:
- Pre-filter for particulate capture
- Hot bypass stack and damper for thermal control
- Independent condenser + dehumidifier system for optimal flow conditions
- Fully integrated VPN remote access for secure diagnostics
- Prewired electrical package to minimize site labor and speed up install
This wasn’t an off-the-shelf system. It was tailored, tested, and tuned for the EPS industry’s unique emission profile.
The Results
⚙️ Plug-and-play readiness — thanks to smart prewiring and full S&SE oversight
🌬️ Clean air confidence — with a verified 98% destruction efficiency
💡 Energy-smart design — 95% thermal efficiency cuts utility costs
🛠️ Ongoing support — remote VPN access keeps the plant covered, even off-hours
✅ Full compliance, zero disruption — mission accomplished
Why It Works: EPS Demands More
EPS manufacturers walk a tightrope. One foot on production. The other on regulation. Pentane emissions are tricky, persistent, and under watch by EPA, AQMD, and other regulatory bodies.
At Ship & Shore, we don’t build “nice-to-have” systems. We build need-it-now solutions. Our 25 years of Clean Air Solutions have helped manufacturers across North America not just meet compliance, but dominate it.
And yes — it’s all Made in America.
From Concept to Compliance to Complete™
This wasn’t just about engineering. It was about trust. Timelines. Technical excellence. And showing up when it mattered. Our motto? Concept to Compliance to Complete™. That’s not just branding — it’s our entire operating model.
You don’t have time for guesswork. We don’t do half-measures.
Let’s move fast. Let’s do it right. Let’s keep your plant running — and the air clean.
Want to See What’s Possible?
👉 Visit our RTO page: https://shipandshore.com/products/regenerative-thermal-oxidizer-rto/
👉 Explore VOC control for EPS: https://shipandshore.com/eps-industry-environmental-update/
👉 Contact us for a review: https://shipandshore.com/contact
Categorised in: Industry news, News, News, Ship & Shore, VOC Abatement