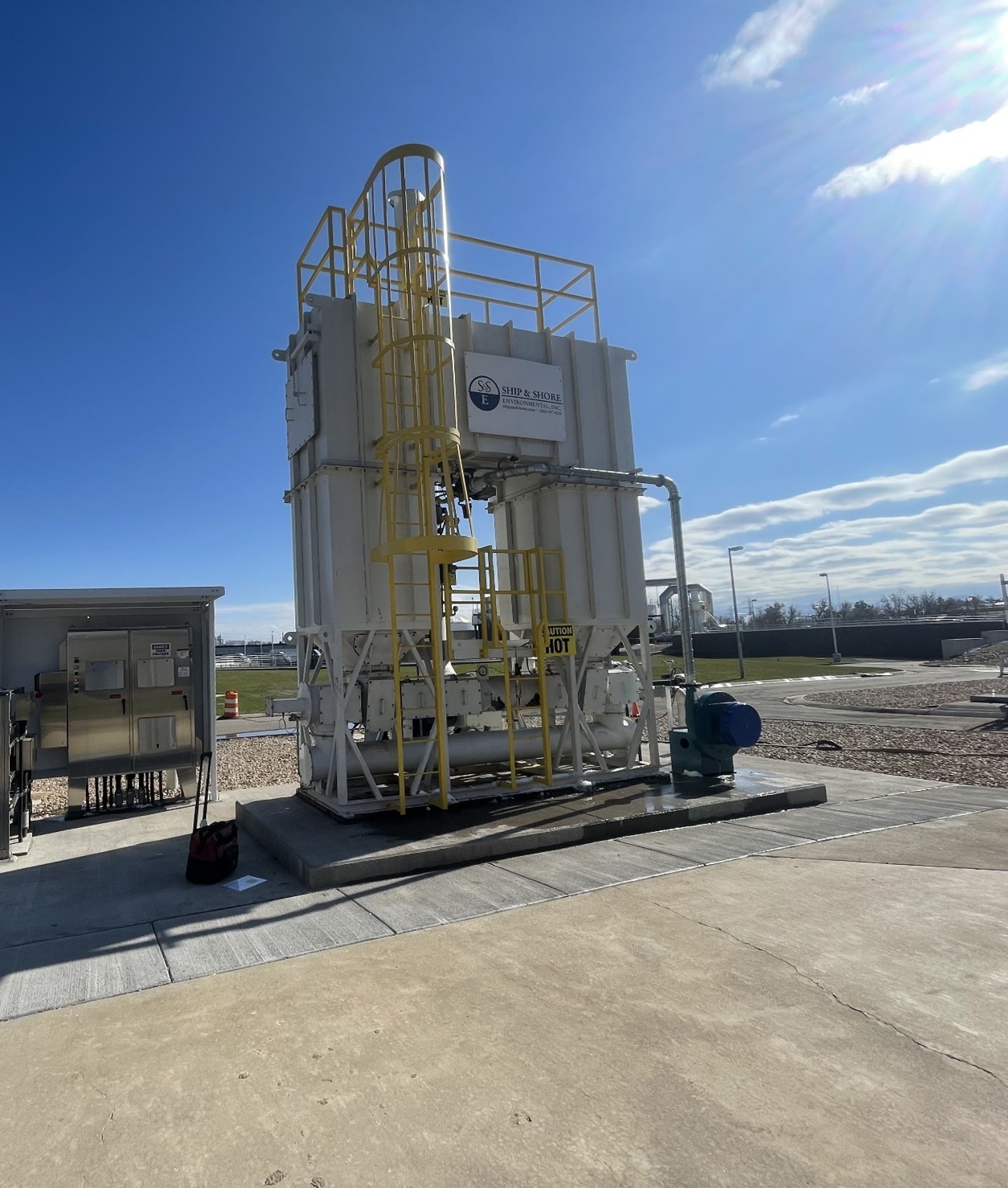
Case Study: Custom Engineered Regenerative Thermal Oxidizer (RTO) for a Biogas Plant
July 9, 2024 11:41 amCase Study: Custom Engineered Regenerative Thermal Oxidizer (RTO) for a Biogas Plant
Client Overview
Our client, a leading biogas company, is dedicated to converting biogas from anaerobic digesters into renewable natural gas (RNG). This transformation supports sustainable energy solutions and aligns with environmental regulations and carbon reduction initiatives.
Challenges
Challenge 1: Off-Gas Treatment
- The facility upgrades biogas by removing impurities such as carbon dioxide, water, and hydrogen sulfide, producing a high-calorific methane stream for injection into the natural gas grid. The low-calorific off-gas separated during this process required effective management to ensure environmental compliance and operational efficiency.
Challenge 2: Emission Control
- To adhere to stringent environmental standards, the facility needed to control emissions of harmful pollutants such as methane (CH4) and carbon monoxide (CO). Additionally, the emission of nitrogen oxides (NOx) needed to be minimized to reduce the environmental impact.
Challenge 3: Operational Efficiency
- The facility required a solution that not only neutralized harmful emissions but also optimized energy recovery and reduced operational costs.
Ship & Shore Environmental’s Solutions
Solution 1: Custom-Engineered RTO System
- Ship & Shore Environmental designed and installed a custom-engineered 15,000 SCFM Regenerative Thermal Oxidizer (RTO) in May 2024. This system was specifically tailored to treat off-gas from the biogas upgrading process.
- Performance: The RTO achieves a 98% destruction efficiency, effectively neutralizing harmful emissions.
- Energy Efficiency: The system’s media ensures approximately 95% thermal effectiveness, optimizing energy recovery and reducing operational costs.
Solution 2: Low NOx Burner Technology
- The RTO is equipped with a low NOx burner, offering specifications of either 80 ppm or 20 ppm, ensuring minimal environmental impact.
- Emission Control: The system maintains CH4 and CO emissions under 100 ppm, adhering to stringent environmental standards.
- Temperature Range: Efficient operation of the RTO within a temperature range of 1,450–1,500°F.
Solution 3: Enhanced System Features
- To ensure reliable and efficient operation, the RTO system includes several advanced features:
- Fan Suction Pressure: Operates under a -2” WC fan suction pressure.
- Pneumatic Cylinder: Enhances reliability and control for the poppet valve.
- LEL Sensors: Two LEL sensors in the RTO inlet stream for precise monitoring.
- ASME Section VIII Pneumatic Air Tank: Equipped with comprehensive instrumentation, including a PSV, pressure indicators, and isolation/drain valves.
- Pre-Wired Unit: Minimizes electrical fieldwork with pre-installed wiring and conduits from the RTO instruments to the junction box and control panel.
Conclusion
This project exemplifies Ship & Shore Environmental’s commitment to providing customized, high-efficiency environmental solutions. The client has purchased a number of systems over the years from Ship & Shore and the successful delivery and installation of the RTO system at the biogas upgrading plant reinforces our role as a trusted engineering and manufacturing partner. We look forward to supporting our client’s future projects with the same dedication and expertise.
For more information on our custom-engineered RTO systems and other environmental solutions, please contact
Ship & Shore Environmental.
Categorised in: Industry news, News, News, Ship & Shore, VOC Abatement