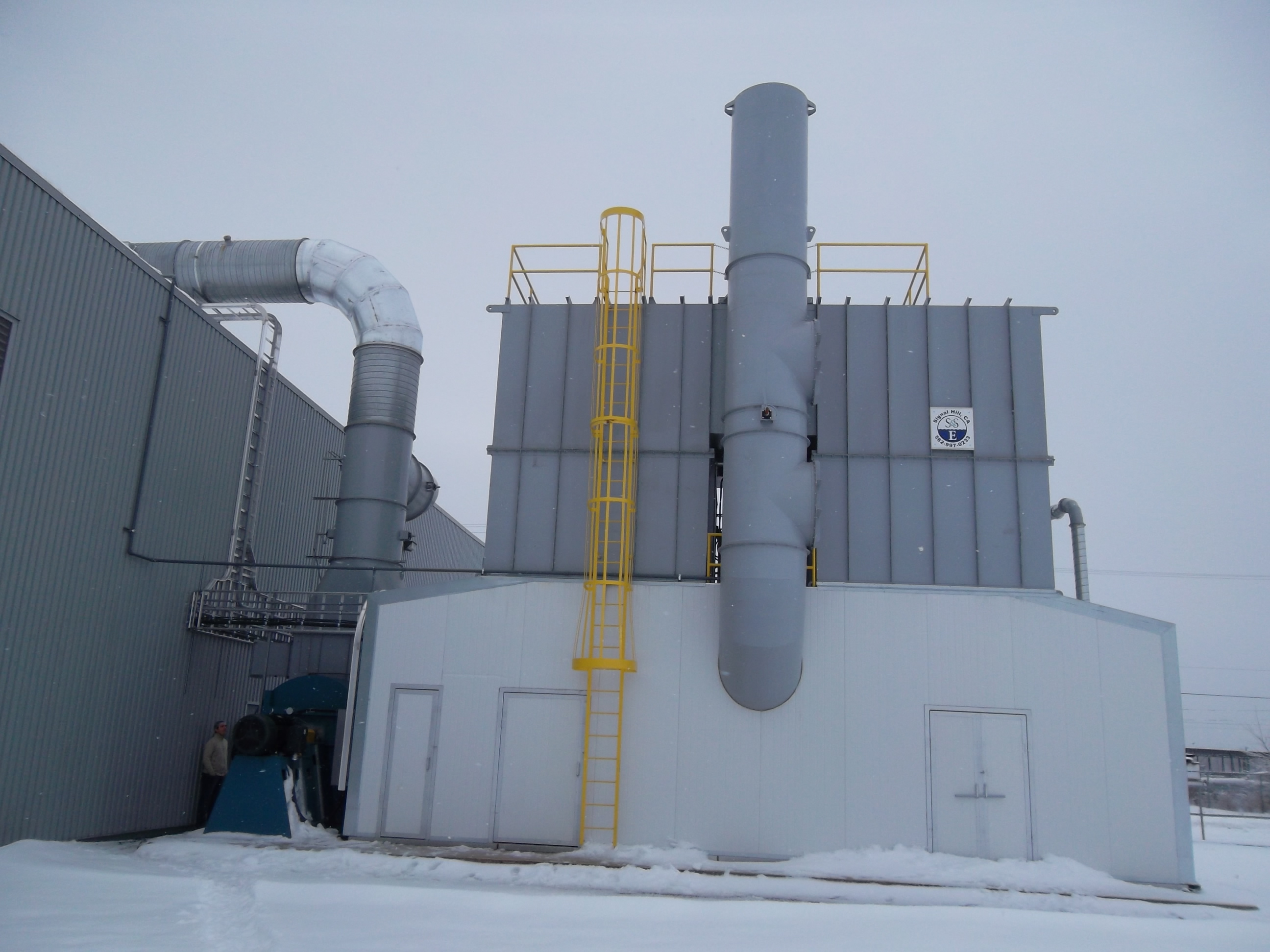
5 Steps To RTO Longevity (Part 1)
November 30, 2016 9:05 am5 Steps To RTO Longevity (Part 1)
1. RTO Proper Construction
Choosing materials that are compatible with the process exhaust constituents can enhance equipment life and ensure excellent performance in corrosive (and normal) process environments. The Regenerative Thermal Oxidizer (RTO’s) shell or inner skin material is generally made of carbon, but stainless steel or even a higher grade alloy such as Hastelloy or Inconel, or the use of a specialty coating can be used to minimize or eliminate corrosion.
The coating or material selection is based on what is either in the process exhaust or the resultant products of combustion, for instance if the VOC contain chlorinated hydrocarbons, a coating would be selected to be resistant to hydrochloric acid.
If a coating is selected its purpose is to prevent the harmful contaminates or products of combustion from reaching housing of the RTO.
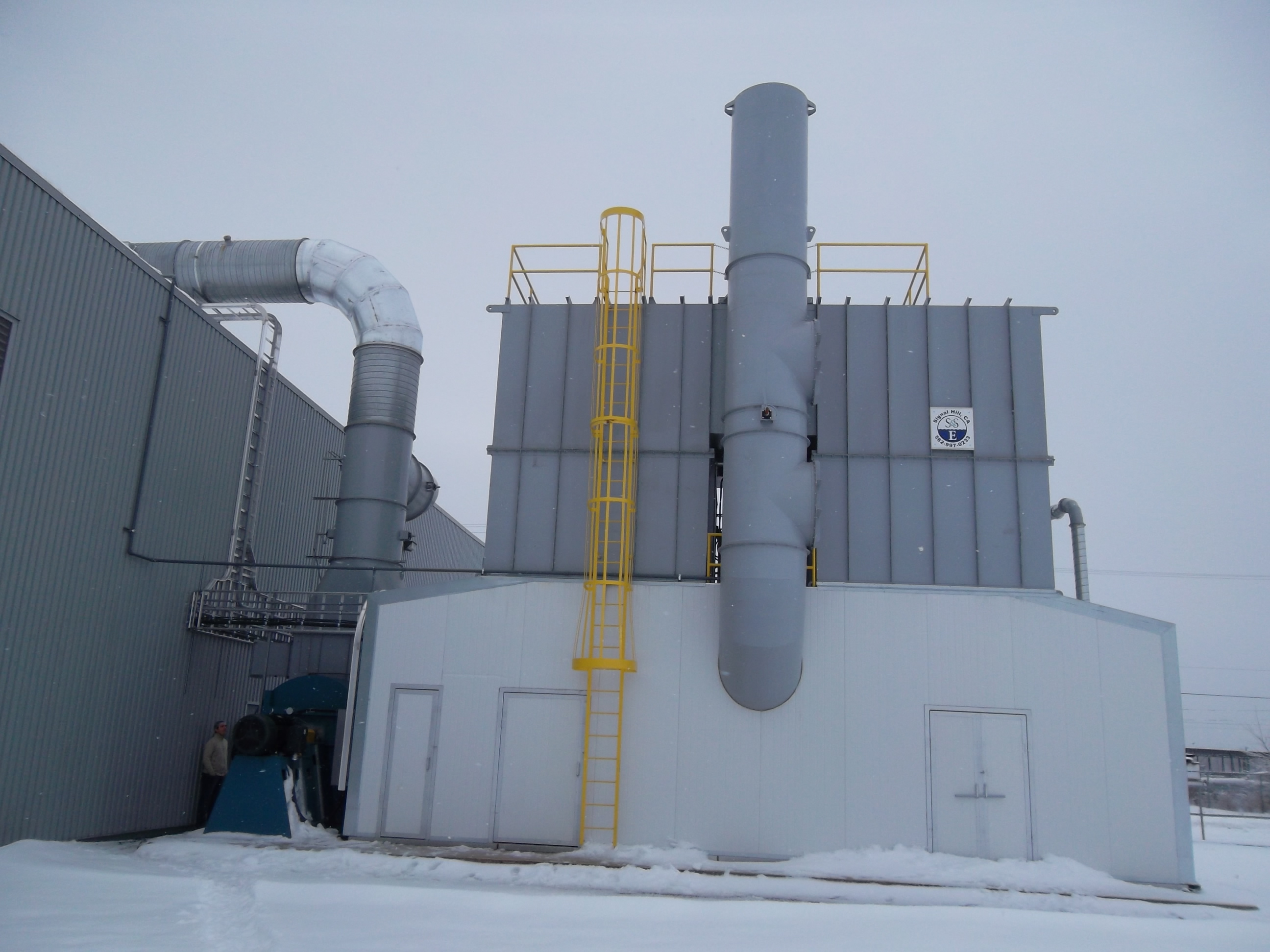
In addition to the construction materials selected, it is critical that care be taken in selecting the right valve. Whether a diverter valve, poppet valve, high quality solenoids, compressors &hydraulics; all will give the equipment greater longevity.
Selecting the right location to install the equipment can reduce equipment downtime and installation costs. Winterization such as heat tracing of important control devices to improve winter time operation is highly recommended. Moreover, installing the unit in close proximity to the process prevents lengthy duct runs, minimizing overall project material and electric utility costs. Regular inspection of sensing lines for cracks, splits, and debris also ensures optimal system performance.
The following tables highlight various process exhaust stream conditions and their possible effect on RTO construction materials.
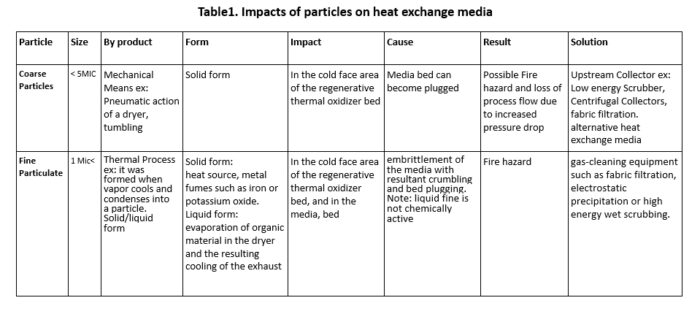
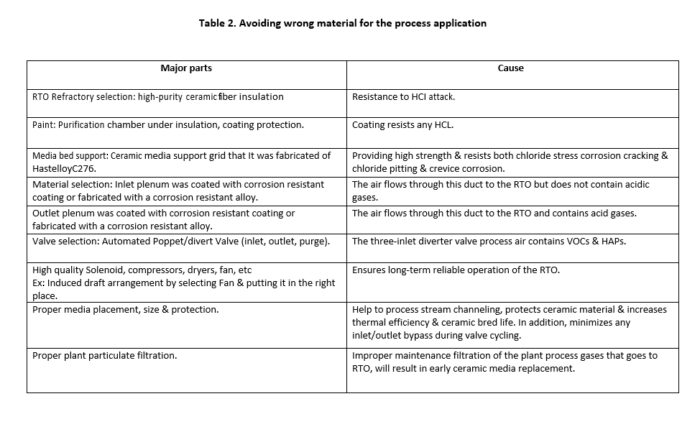
Call our Experts for a Free & Confidential Initial Consultation based on your needs 562-997-0233.
Categorised in: Green Energy, Industry news, RTO, Ship & Shore