10 Steps to determine RTO capacity when expanding manufacturing operations
February 18, 2015 6:43 pm10 Steps to Determine RTO Capacity when Expanding Manufacturing Operations
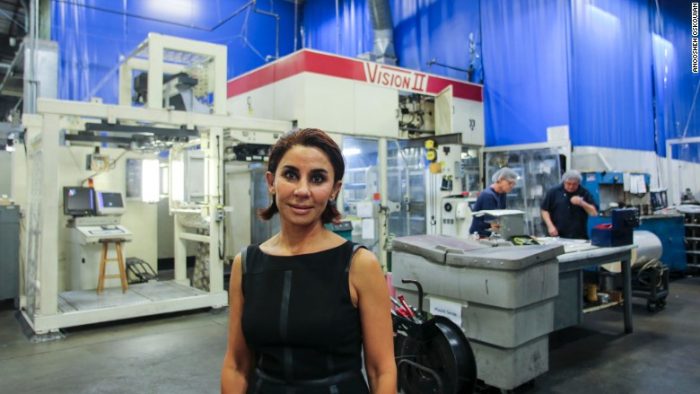
Complying with government regulations can be overwhelming. Especially, when you are attending to your business and customer needs. Implementation of an RTO project has profound environmental, regulatory and financial considerations for any business. There are many cash incentive/rebate programs that can pay for up to 50% of the project and are typically in excess of $100,000.
In this first step you will conduct an inventory of all the processes that emit air contaminants at your facility. An explanation of how to conduct an inventory is explained below. First, draw a plan view of your facility. A facility may have a fixed location (e.g., factory, plant, or commercial establishment) or may be movable (e.g., concrete crusher). Operations located across the street from one another may also be part of the same facility if they are: Located on connected or adjacent pieces of property; under control by the same owner; and belong to the same industrial grouping .
Next, identify the emission sources. These are the processes at your facility (such as boilers, spray paint booths, de-greasers, and generators) that generate air pollutants. If you have any air permits, use them to help identify your emission sources . Even though some of your operations may not directly emit contaminants to the outside through a stack or vent, the emissions will eventually exhaust into the atmosphere through building ventilation or escape through doors or windows. These types of emissions must be included in your calculations . Be sure to include any processes not located in your main building. If you have a standby generator, storage silo, or other equipment located on your property but away from the main building, it is still part of the facility. You may also have equipment that you do not operate anymore. If this equipment is still able to operate, it is considered a process. If these processes are still operable, they must be included in your PTE calculation.
We understand what it takes, and know that you want to get it right the first time. We can walk with you through the process. Utilize our team of experts to collect and analyze the data, correctly select the best equipment, and make your project a success.
Categorised in: Case Study & White Papers