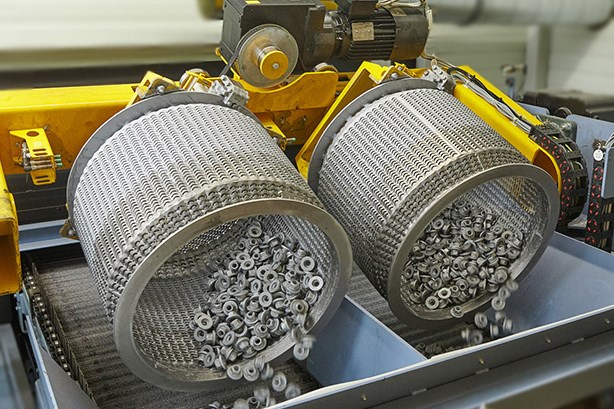
#TechTalk – Controlling emissions from Dip Spin Coating Process
September 11, 2024 9:18 am#TechTalk - Controlling emissions from Dip Spin Coating Process
The dip spin painting process can be viewed as a very simplistic operation to provide decorative and corrosion resistant coatings within the fastener industry. Depending on choice of coatings, there may be a need for air pollution control equipment to meet Federal and State volatile organic compound (VOC) removal requirements. In larger coating operations VOC emissions could eclipse limits and trigger the need for abatement.
Regenerative Thermal Oxidizers (RTOs) are typically used to treat these emissions due to their high destruction efficiency and extremely high thermal efficiency.
Typical dip spin coating system is comprised of the following processes:
- Paint Storage and Mixing rooms
- Parts Cleaning
- Dip Spin Coating Process
- Parts Curing (and cooling)
Generally, regulatory authorities target the coating process, oven curing operations, and potential emissions from paint storage and mix areas to maximize collection of emissions from the system. The collection system implements a network of ductwork to capture and direct the emissions to a destruction device (RTO). The collection system may also include paint particulate filtration to capture materials that could foul VOC treatment equipment.
Once parts are cleaned and dried, parts are placed in a wire mesh basket and submerged into a desired coating bath. Once coated in the paint bath, the mesh basket is elevated and rotated to distribute the coating onto the parts centrifugally and drive excess paint material off the parts to drain back into the bath. Depending on finish specifications, immersion time, basket size, spin speed/reverse spin, spin time, part load, and viscosity of the paint will impact quality. Solvent emissions are generated during the coating process.
Painted parts are then removed to the oven curing area. Parts are dumped onto a conveyor / shaker table to spread parts for uniform curing. Additional emissions are also released into the atmosphere in this area.
Freshly painted parts now enter the oven to cure. Multiple zone oven heating is used to uniformly elevate the part temperature, driving off all moisture/solvent to be exhausted via fans out of the plant. Ovens account for the highest capture of VOC within the system.
Best abatement system design will capture emissions from paint storage / mix, paint dip enclosure, part dump and shake, and the curing ovens. As mentioned previously, RTO technology is extremely effective in controlling the large volume of air possible (for treatment) with a more dilute solvent concentration typical. The extremely high thermal efficiency of the RTO ceramic heat exchangers enables the RTO to achieve desired destruction efficiency while minimizing natural gas fuel consumption by the oxidizer burner (typically operating at 1450 to 1500 degrees F). And in many instances, the BTU value contained in the process exhaust can fuel the RTO on its own to allow the NG burner to operate in pilot or in reduced condition.
As an added benefit, RTO technology qualifies for natural gas rebate incentives from qualifying utility providers. Ship & Shore will work on the customers behalf to secure these incentives if available.
Ship & Shore Environmental routinely works with dip spin OEM equipment suppliers and end customers to design best cost effective abatement systems.
Categorised in: Industry news, News, News, Ship & Shore, TechTalk