High-Cycle Valves in Regenerative Thermal Oxidizers
High-Cycle Valves in Regenerative Thermal Oxidizers
Regenerative Thermal Oxidizers (RTOs) are regularly utilized in the industry to collect and control air pollution emissions generated from industrial manufacturing operations. For the last decade, a lot of emphasis has been laid on the selection of the ceramic media and burners for the RTOs while the most critical piece of the RTO operation – High Cycle Valves – has been overlooked.
Generally, two kinds of valves are used in RTOs. High-cycle valves are connected directly to the RTO’s heat-exchanger canisters, directing the flow of process air into and out of the canisters, which need to open and close every few minutes (typically 1 to 3 minutes) on a continuous basis. Most other valves associated with RTOs are called low-cycle valves due to their lower cycling frequency. Examples of low cycle valves include isolation and diverter valves.
The following focuses exclusively on high-cycle valves, which are critical to the overall performance of an RTO — namely to achieving high destruction efficiencies. RTO designs can be classified into three categories: single-canister, odd-canister, and even-canister designs. The style of high-cycle valve used is determined by the canister design.
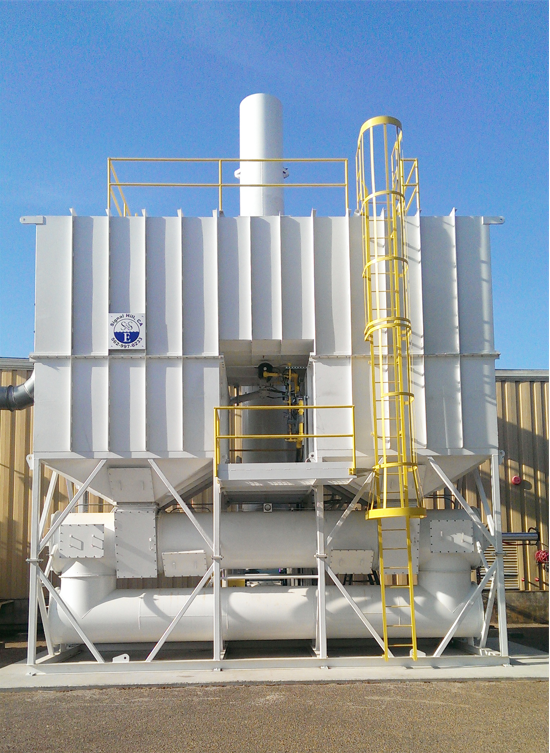
This two-canister regenerative thermal oxidizer (RTO) is equipped with high-cycle horizontal poppet valves
High-Cycle Valves Overview
High-cycle valves are critical to the overall performance of an RTO. They are important for:
- High destruction efficiencies
- Directing the flow of process air into and out of the canisters
Some commonly available high-cycle valve designs used in RTOs include the following:
- Butterfly valves (including single-blade, dual-blade and dual-seat valves)
- Poppet valves (including single poppet, dual poppet and four-way poppet valves)
- Single-canister rotary valve
- Two-canister, high cycle, rotating-flow reversal indexing valve
Other important points to consider when selecting high cycle valves for RTO applications:
- Valve seat material — options include metal-to-metal seats or ceramic (soft)
- Valve actuation mode — options include hydraulic, pneumatic, or electric
- Maximum allowable leakage rate — typically 0 to 0.25%
- Materials of construction
- Resistance to condensable organics and other particulate matter
Types of High-Cycle Valves
Butterfly Valves
High-cycle butterfly valves have been used in RTOs for more than 40 years. Consisting of a heavy-gauge flat plate inserted into a gas stream, the high cycle valve plate is rotated by means of a motor (actuator) and linkage to control the gas-stream flow. When the valve is in the fully open position, the flat plate is aligned with the direction of gas flow and, therefore, provides very little flow restriction.
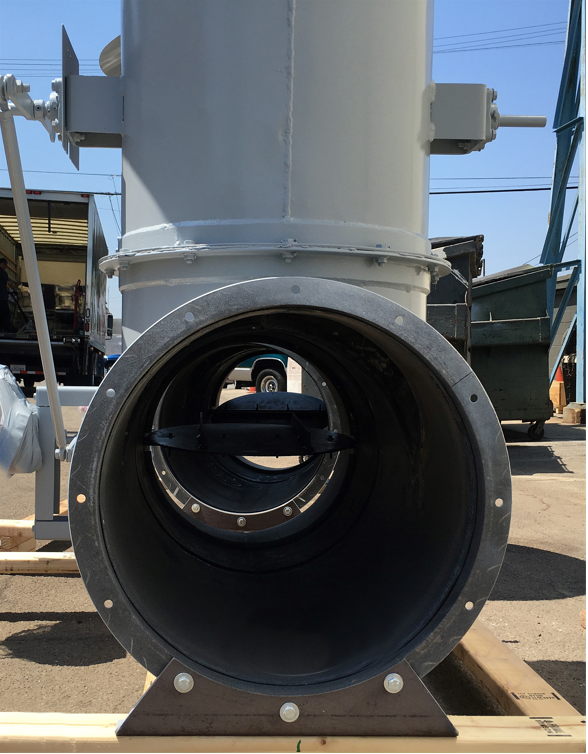
High-cycle butterfly valves used in RTOs will employ a flat valve plate that is mechanically rotated to control gas flow
Butterfly Valve Design
- Occupies less space than any other valve style
- Broad versatility
- Relatively tight sealing
- Offer a simple and reliable means of gas control for both modulating and on-off type applications
- Center-mounted rotating disc/discs that typically rotate 90 degrees
- Type and size of the valve dictates the torque and actuation requirements
- Single blade valve consists of a single solid disc (or blade) that seats against a metal or a compressible-bulb (ceramic) seal
- Double-blade valve is used when zero leakage is required
High-Cycle Poppet Valves
Throughout the U.S. and in Europe, poppet valves have been used for over 25 years in two- and multi-canister RTOs. They consist of a flat circular plate that is raised or lowered typically by an electrical or pneumatic actuator. When the flat plate is in the closed position, it provides a gas seal by pressing against a raised circular seat. Gas attempting to pass through the cylinder is blocked. When the valve disk moves laterally, there are 12 to 24 in. between its open and closed position.
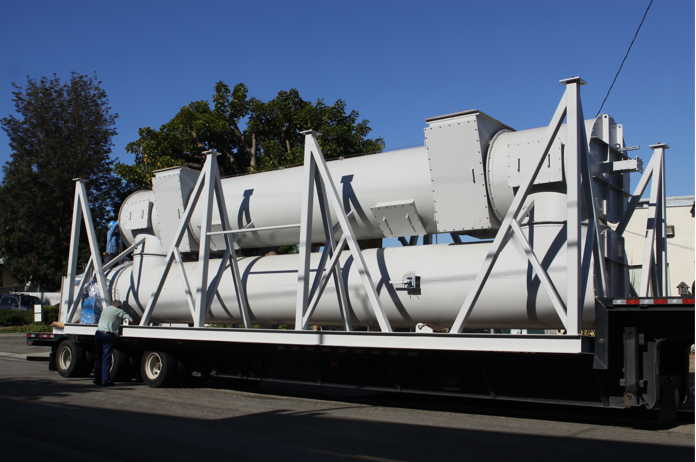
High-cycle poppet valve systems are designed for on-off control, rather than modulating applications
High-Cycle Poppet Valve Design
- System-outlet poppets are single-disc, low leak model
- System bypass poppets are leak-free and employ a double blade and seat with sealed air
- Valves range from 20-60 in. in diameter for industrial baghouses
- Valves range from 48 to over 96 in. in diameter for power-generation baghouses
- Two-way poppets should have one inlet and one outlet damper providing fail-safe conditions during power outages and upset operating conditions
Single-Canister Rotary Valves
The single-canister rotary valve design eliminates the need for separate inlet, outlet, and purge valves by replacing them with a single large valve. Rotary valve designs have been applied to RTOs for over 20 years. The sequence of the bed function as an inlet, outlet or purge is achieved by the rotation of this single valve. This valve is located below the heat recovery chambers and is either electrically or hydraulically driven.
Single-Canister Rotary Valve Design
- Eliminates need for separate inlet, outlet, and purge valves
- Single valve moves at several minutes per rotation and ensures a smooth transition from inlet-to-purge to outlet-to-purge
- Utilizes a machined metal-to-metal surface for tight sealing
Flow-Reversal Indexing Valves
Conversely, another valve type — high-cycle flow-reversal indexing valves — can offer zero leakage in an assembly that has only one moving part. Each 90-deg index rotation of the shaft-interconnected flow diverter assembly reverses flow through the valve and interconnected RTO system.
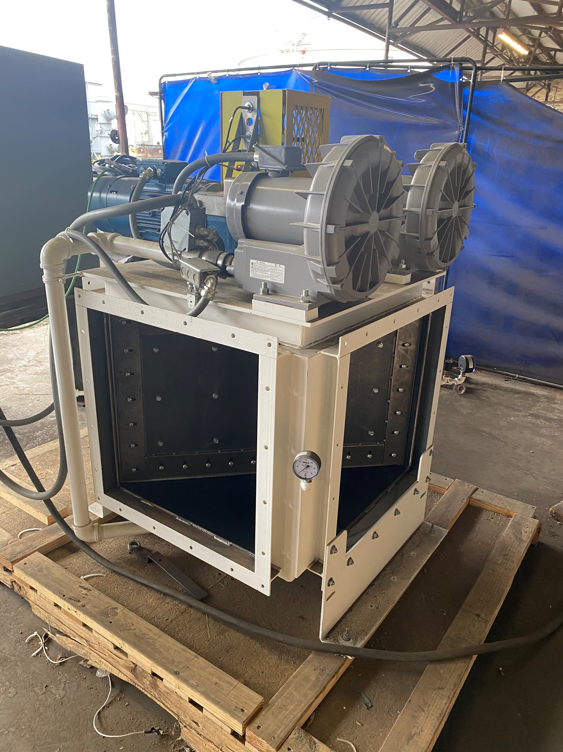
A flow-reversal indexing valve provides a zero-leakage design that utilizes a high-pressure air sealmodulating applications
Flow-Reversal Indexing Valve Design
- Can offer zero leakage
- Requires no duct manifolds
- Equipped with one duct-mounting flange on each of its four ports
- Each rotation valve movement (typically less than 0.5 s) reverses flow through the RTO
- Sealed using high-pressure air
Read the original article here by our COO Anu Vij.
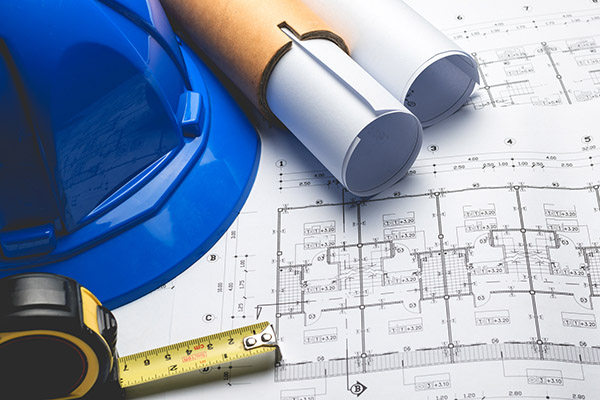